Паровой риформинг метана — Производство водорода
Air Liquide Engineering & Construction предоставляет технологию парового риформинга метана (SMR) для производства водорода как в больших, там и в малых объемах. SMR – экономически и энергетически эффективный способ получения водорода. Высокая степень чистоты достигается за счет использования собственной установки водородной КЦА.
В процессе парового риформинга обессеренное углеводородное сырье (природный газ, отходящий газ, ШФЛУ или нафта) подогревается, смешивается с паром и опционально подвергается конверсии перед подачей на катализаторы в запатентованной установке парового риформинга с верхним пламенем. При этом получаются следующие продукты: водород, монооксид углерода (CO) и диоксид углерода (CO2). Смесь CO с паром подвергается конверсии, продуктами которой являются дополнительный водород и CO2. Затем водород отделяется путем адсорбции в водородной КЦА.
Преимущества от водородной технологии для заказчика
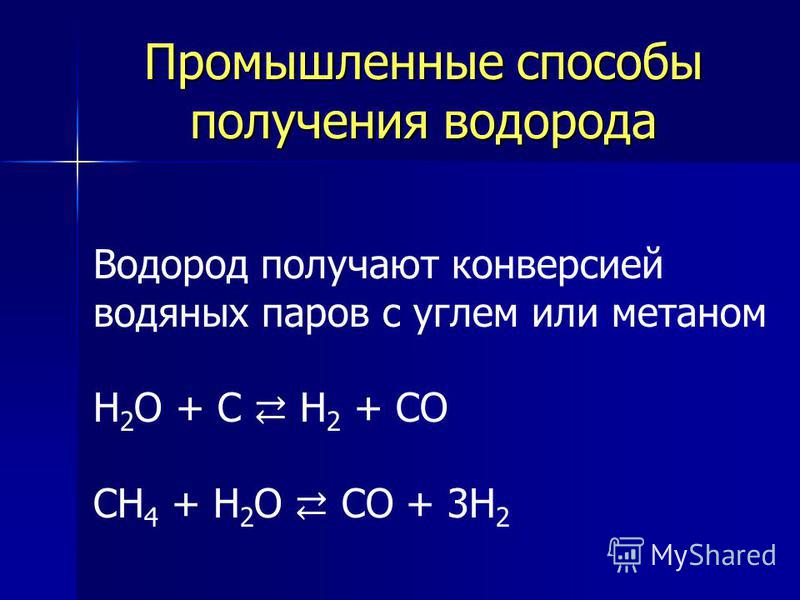
В случае необходимости производства небольших объемов водорода Air Liquide Engineering & Construction предлагает подход к SMR с поставкой высокомодульного стандартизированного оборудования, основными чертами которого являются компактное расположение и исполнение в четырех типоразмерах с использованием заранее выбранного оборудования, разводки трубопроводов и модулей.
Преимущества
- Возможности различной степени адаптации оборудования для удовлетворения требований заказчика
- Упор на лучшую в данном классе эксплуатационную готовность и надежность установки, обеспечиваемые эксплуатационным опытом Air Liquide
- Специальная стандартная программа для установок с малой производительностью водорода с высокой степенью модульности делает возможным срок исполнения менее 15 месяцев на условиях FOB
Основные показатели
- Производительность: 10 000–200 000 нормальных кубических метров водорода в час (Нм³/ч) (10 000–40 000 Нм³/ч для стандартных небольших установок)
- Сырье+топливо-пар: 12,3–13,2 мегаджоулей на нормальный кубический метр (МДж/Нм³)
- Производство пара: 0,4–1,2 килограмма на нормальный кубический метр водорода (кг/Нм³)
Климатически нейтральный водород из природного газа | by Vladimir Sidorovich | Internet of Energy
Начат проект по экологически чистому промышленному пиролизу метана.

В энергетических дебатах водород все чаще рассматривается как ключ к успеху энергетического перехода. Эксперты из Международного энергетического агентства IEA подсчитали, что добавление всего 20% водорода в европейскую газовую сеть приведет к сокращению выбросов CO2 на 60 миллионов тонн в год. Это столько, сколько Дания эмитирует за целый год.
Когда мы рассуждаем об экологически чистом, «зеленом» водороде, обычно подразумеваем электролиз на основе возобновляемой электроэнергии. Однако, судя по всему, есть и другой путь.
Исследователи из Технологического института Карлсруэ (KIT) в Германии разработали «особо эффективный» процесс пиролиза метана, и вместе с промышленным партнером Wintershall Dea в настоящее время дорабатывают его для использования в индустриальных масштабах.
Пиролиз метана позволит использовать ископаемый природный газ без вреда для окружающей среды: метан будет разделяться на газообразный водород и твердый углерод, который является ценным сырьем для различных отраслей промышленности и также может безопасно храниться.
«Прямой термический крекинг метана и других углеводородов обеспечивает способ получения водорода из природного газа без прямых выбросов CO2», — объясняет профессор Томас Ветцель из Института технологического проектирования в KIT. Его исследовательская группа совместно с Институтом перспективных исследований в области устойчивого развития в Потсдаме разработала метод, в котором метан непрерывно разлагается на его компоненты — водород и твердый углерод — в барботажной реакторной колонне, заполненной жидким металлом.
В рамках совместного проекта, запланированного на три года, KIT и Wintershall Dea хотят заложить основы будущего промышленного использования пиролиза метана. «В мире существует большое количество природного газа, и существует возможность его использования без климатического воздействия. В нашем исследовательском проекте мы хотим изучить, как нам реализовать задуманное технически эффективно и на больших объёмах газа», — говорит Ветцель. «Природный газ уже сегодня является самым чистым традиционным источником энергии, но он может стать еще более благоприятным для климата в будущем — путем отделения CO2 и извлечения водорода», — говорит Хуго Дейкграаф, член правления и главный технический директор Wintershall Dea.
Об экономике проекта ничего не сообщается. Видимо, на нынешней ранней стадии о ней говорить преждевременно. Учитывать в ней необходимо также и использование получаемого технического углерода.
Более того, две описанные особенности технологии вызывают серьезные сомнения в возможности сделать ее конкурентоспособной. Во-первых, в реакторах разложение метана осуществляется в среде жидкого олова при температуре 1175°С, а работе с жидкими металлами, как известно, усложняет и удорожает процесс и с точки зрения его аппаратной реализации, и с точки зрения обслуживания и безопасной эксплуатации. Во-вторых, используемая в процессе производства водорода реакция разложения метана — эндотермическая, и кроме энергии, запасенной в самом метане, к ней необходимо подводить за счет нагревания дополнительно 75 кДж/моль энергии, которая для получения “зеленого” водорода должны быть электрической или получаться из сжигания части получаемого водорода. Этот фактор приведет к снижению эффективности преобразования энергии метана в водород. Вместе указанные две особенности технологии делают сомнительным возможность достижения конкурентоспособных показателей стоимости водорода (LCOH), полученного этим методом.
Тем не менее, эта технология может сыграть в итоге существенную роль в превращении ископаемого углеводородного топлива в ресурсную базу для полностью декарбонизированной водородной энергетики.
Подготовлено IC ENERGYNET.
Авторы: Владимир Сидорович, Игорь Чаусов.
Расплавы металлов разложили метан на углерод и водород без побочных продуктов
Brian Long / University of California, Santa Barbara
Американские химики-технологи разработали каталитическую колонну, в которой расплав металлов превращает метан в водород и углерод без образования побочных продуктов.
Основной проблемой получения чистого водорода с помощью паровой конверсии метана является образование в ходе реакции углекислого газа. Когда этот процесс только разрабатывался, образование углекислого газа в качестве одного из продуктов реакции не считалось проблемой, однако сейчас из-за постоянного роста концентрации CO
Для решения этой проблемы группа химиков-технологов из Калифорнийского университета в Санта-Барбаре под руководством Эрика Макфарланда (Eric W. McFarland) предложила схему каталитической колонны высотой чуть больше одного метра, в которую катализатор помещается в виде расплава при температуре около 1000 градусов. Через этот расплав продуваются пузырьки метана, которые постепенно превращаются в водород и углерод. Образующийся уголь всплывает на поверхность расплава, где может быть собран и удален из реакционной зоны.
В качестве катализаторов такой реакции ученые использовали расплавы металлов и их сплавов, в которых активным компонентом являются переходные и благородные металлы. В своей работе химики сравнили активность расплавов различных катализаторов пиролиза метана, и наиболее эффективным катализатором в такой каталитической системе оказался сплав, содержащий 27 процентов никеля и 73 процента висмута. Активным компонентом в такой системе является никель, а висмут выполняет роль своеобразного «растворителя».
Для объяснения активности катализатора авторы работы провели компьютерное моделирование расплава металла, через который двигаются молекулы метана. Оказалось, что атомы активного компонента катализатора (например, никеля или платины) находятся в материале в виде отрицательно заряженных ионов, эффективный заряд которых и определяет каталитическую активность материала. А он в свою очередь сильно зависит от свойств металла-растворителя, в частности, его температуры плавления.
С помощью такой каталитической системы удалось провести конверсию метана с эффективностью около 95 процентов, которая не снижается и при повышении давления газа до примерно двух атмосфер. Поэтому уже в ближайшее время такие системы можно будет использовать для дешевого и экологически безвредного получения чистого водорода из метана.
В случае, если углерод является побочным продуктом реакции, а не основным, то его осаждение на поверхность катализатора можно предотвратить с помощью небольшого изменения химического состава катализатора. Например, если добавить в никелевый катализатор олово, то оно встраивается в те позиции, куда мог бы осаждаться углерод и таким образом сильно замедляет возможную пассивацию.
Александр Дубов
Замглавы «Газпрома» предложил смешивать природный газ с водородом :: Экономика :: РБК
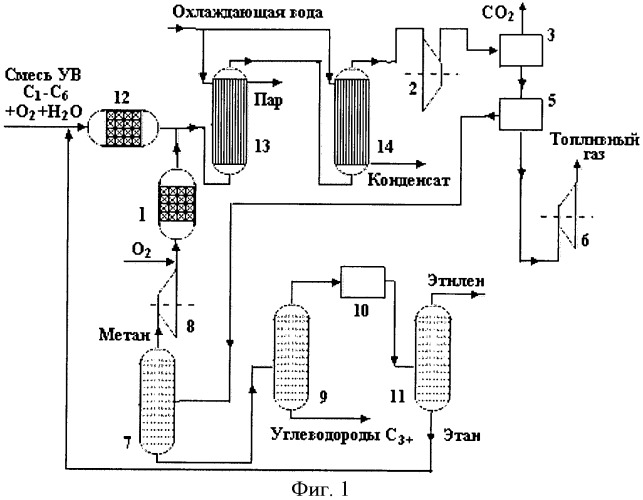
«Никаких отрицательных последствий подмешивания водорода в природный газ, начиная от этапа транспортировки газа до его потребления в электрогенерации и промышленности, нет», — сказал Медведев, отвечая на вопрос о том, как повлияет добавление водорода к природному газу на качество топлива и на возможность его прокачки по газопроводам.
Читайте на РБК Pro
Медведев также отметил, что необходимость применять чистый природный газ сохраняется в некоторых областях газохимического производства. Эта проблема может быть решена с помощью технологий по выделению водорода после транспортировки газоводородной смеси по трубопроводам или если будет частично сохранена возможность транспортировки природного газа в чистом виде, считает он.
«Международное и межкорпоративное сотрудничество по этой теме уже ведется. Это может стать мировой темой сотрудничества не только с Европой, но и с Японией, Южной Кореей и даже США», — отметил Медведев, обратившись к замминистра энергетики Павлу Сорокину.
Комментируя выступление Медведева, Сорокин отметил, что Россия поддерживает Парижское соглашение по климату, однако напомнил, что «гигантские запасы газа», которыми обладает Россия, должны быть монетизированы. «Учитывая, что через 30–40 лет ресурсная рента от углеводородов, которую мы будем получать, будет намного меньше, чем сейчас, мы смотрим на ускоренную монетизацию наших углеводородов», — сказал Сорокин.
«Идея Александра Ивановича [Медведева] — одна из тех, что мы всерьез рассматриваем. Мы готовы включить ее в повестку ближайшего совещания у председателя правительства», — заключил он.
«Газпром» запатентовал и тестирует способ получения водорода из метана с применением адиабатической конверсии при использовании метано-водородной смеси на собственные нужды на компрессорных станциях при газопроводах, пояснил РБК доцент кафедры экономики региональной энергетики и энергоэффективности РГУ нефти и газа им. Губкина Владислав Карасевич.
По его словам, сейчас в России проходит испытания установка на 1000 куб. м газа в час. «У метано-водородной смеси есть преимущества — за счет производства смеси уменьшается потребление метана на турбине (сегодня состав смеси составляет 80 на 20% в пользу метана). Кроме того, при использовании смеси на 30% снижаются выбросы CO2, что при постоянном росте их стоимости (сейчас это €30 за тонну для стран ЕС) делает использование данных технологий интересным для зарубежных проектов», — добавил эксперт.
По мнению Кирилла Лятса, совладельца компании «СПГ-Горская» (строит СПГ-завод в Ленинградской области мощностью 1,26 млн т), смесь водорода с метаном будет стоить дороже, чем просто природный газ. По его мнению, под прокачку такой смеси придется модернизировать действующие экспортные газопроводы или перестраивать новые с затратами до половины выше текущей стоимости. «Все сварочные швы трубопроводов необходимо будет проверять рентгеном, чтобы не допустить даже возможности взрыва такой смеси. Для прокачки обычного газа достаточно испытаний с использованием химического раствора», — пояснил эксперт. Также должны быть построены более сложные и дорогостоящие газораспределительные и компрессорные станции. Он также добавил: «Получение водорода путем риформинга природного газа влечет за собой выбросы в атмосферу CO₂ в месте его производства, что делает использование такой смеси нелогичным в экологических целях. Кроме того, при ее изготовлении из газа не убираются такие примеси, как сера, которые при попадании в атмосферу тоже вредят экологии».
Фонд Билла Гейтса инвестирует в пиролиз метана
Breakthrough Energy Ventures, фонд, принадлежащий Биллу Гейтсу, возглавил раунд финансирования в размере 11,5 миллионов долларов США для калифорнийского стартапа C-Zero Inc. Средства были привлечены также от подразделения итальянской нефтегазовой компании Eni Next, Mitsubishi Heavy Industries и AP Ventures.
По собственному заявлению C-Zero, её технология – это «форма пиролиза метана, в которой используется инновационный термокатализ для извлечения углерода из природного газа в виде плотного твердого вещества». Компания разрабатывает «систему декарбонизации, которую можно поместить между существующей газовой инфраструктурой и промышленными потребителями природного газа, стремящимися снизить выбросы углекислого газа».
Разделить метан, состоящий из одного атома углерода и четырех атомов водорода, на водород и твердый углерод не сложно с точки зрения химии. Основная задача сейчас — снизить стоимость при расширении масштабов технологии.
C-Zero может производить около 10 кг водорода в день на небольшой экспериментальной установке. Следующим шагом является создание демонстрационной установки, способной производить 100 кг газа в день, а затем коммерческой установки, способной производить более 1000 кг газа в день. Большинство стартапов в области чистой энергии терпят неудачу на этапе масштабирования, отмечает Bloomberg.
«Мы рады вступить в следующий этап роста компании при поддержке инвесторов, которые разделяют наше желание масштабировать технологию с потенциалом декарбонизации более четверти мирового потребления энергии», — сказал Зак Джонс, генеральный директор C-Zero. «Превратив природный газ в чистый водород, … мы надеемся стать мостом между существующей газовой инфраструктурой и низкоуглеродным будущим».
Сегодня большая часть водорода в мире производится из природного газа. Однако при использовании нынешнего метода (паровой риформинг метана) в атмосферу выбрасывается большое количество диоксида углерода. Поэтому многие заинтересованные стороны работают над стимулированием развития технологий улавливания углерода, в результате работы которых CO₂ будет закачиваться глубоко под землю. В частности, в июле 2020 года норвежский Equinor представил план крупнейшего в Европе завода по производству «синего водорода».
Джонс утверждает, что гораздо лучше иметь дело с твердым углеродом, чем беспокоиться о захороненном газе CO₂. Кроме того, он прогнозирует, что его «пиролизный», или, как его ещё называют, «бирюзовый» водород будет дешевле синего.
«Пиролиз метана очень интересен для нас, поскольку чистый водород с низким содержанием CO2 может быть произведен с ограниченным потреблением энергии и без использования воды. Расширение масштабов этого процесса потенциально будет огромным преимуществом для производства водорода для энергетики или химической промышленности», — отметил представитель Eni Next. Да, отсутствие потребления воды может рассматриваться в качестве одного из потенциальных конкурентных преимуществ пиролиза.
Над технологией пиролиза работают и другие компании, в том числе такие гиганты как BASF и Газпром, но она пока ещё сыровата.
Читайте также: «Производители обещают резкое снижение цен на электролизеры и зеленый водород».
Уважаемые читатели!
Ваша поддержка очень важна для существования и развития RenEn, ведущего русскоязычного Интернет-сайта в области «новой энергетики». Помогите, чем можете, пожалуйста.
Яндекс Кошелёк
QIWI Кошелёк
Карта Сбербанка: 4276 3801 2452 1241
Получение углеродного наноматериала и водорода из природного газа под действием сверхвысокочастотного излучения Текст научной статьи по специальности «Химические науки»
■ НАШ САЙТ В ИНТЕРНЕТЕ: WWW.GAZOHIMIYA.RU
НАНОТЕХНОЛОГИИ Я
ПОЛУЧЕНИЕ УГЛЕРОДНОГО НАНОМАТЕРИАЛА И ВОДОРОДА ИЗ ПРИРОДНОГО ГАЗА ПОД ДЕЙСТВИЕМ СВЕРХВЫСОКОЧАСТОТНОГО ИЗЛУЧЕНИЯ
А.Г. ЖЕРЛИЦЫН, В.П. ШИЯН
НАУЧНО-ИССЛЕДОВАТЕЛЬСКИЙ ИНСТИТУТ ЯДЕРНОЙ ФИЗИКИ ПРИ ТОМСКОМ ПОЛИТЕХНИЧЕСКОМ УНИВЕРСИТЕТЕ Ю.В. МЕДВЕДЕВ, С.И. ГАЛАНОВ, О.И. СИДОРОВА
ТОМСКИЙ ГОСУДАРСТВЕННЫЙ УНИВЕРСИТЕТ
Необходимость глубокой переработки углеводородного сырья и требования сегодняшнего дня к утилизации природного и попутного газов, в состав которых входит до 95-97 % метана, определяют повышенный интерес производителей к конверсии природного газа в углерод и водород. Одним из традиционных способов осуществления эндотермической реакции разложения метана на углерод и водород является высокотемпературный пиролиз. Для его реализации требуются высокие (800-1200 °С) температуры, при этом весьма широк спектр получаемых продуктов реакции, а степень конверсии метана достигает 12-20 %. В последние годы отмечен повышенный интерес к проблеме конверсии метана с использованием электромагнитного излучения сверхвысокочастотного (СВЧ) диапазона. При этом в ряде работ зафиксировано повышение степени конверсии метана в присутствии СВЧ-поля [1]. Большое внимание при реализации данного процесса уделяется подбору гетерогенного катализатора, который бы эффективно взаимодействовал с СВЧ-полем. Так, в работе [2] предпринята попытка выяснения механизма влияния СВЧ-газового разряда и, соответственно, СВЧ-излучения на скорость образования ацетилена из метана для трех групп твердых катализаторов: нанесенные металлические катализаторы, массивные металлы, углеродсодержащие объекты.
Эксперименты, проведенные на нанесенных на диэлектрик никельсодержащих катализаторах и
металлических (Ni, Cu, Fe) сетках, позволили оценить степень поглощения СВЧ-мощности этими объектами, но не дали ответа о механизме воздействия СВЧ-излучения на пиролиз метана. В работе [3] рассмотрен процесс термического разложения метана на водород и углерод при воздействии плазмы микроволнового импульсно-периодического псевдокоронного разряда
атмосферного давления на предварительно нагретый метан. Отмеченное в данной работе ускорение реакции при воздействии разряда объясняется генерацией плазмой СВЧ-разряда химически активных частиц, способствующих разложению метана. Приведенные примеры демонстрируют повышенный интерес исследователей к использованию электромагнитного
ГАЗОХИМИЯ 39
Я НАНОТЕХНОЛОГИИ
Рис. 1
Схема установки
1 — источник СВЧ-излучения; 2 — камера с катализатором; 3 — разрядная камера; 4 — окно; 5 — агломератор;
6 — фильтры
излучения СВЧ-диапазона для интенсификации химико-технологических процессов.
В настоящей работе рассматривается принципиально новый способ конверсии природного газа в углерод и водород, основанный на совмещенном воздействии на природный газ катализатора и СВЧ-поля [4, 5]. В ходе реализации данного способа получены наноразмерные углеродные материалы (нанотрубки и аморфный углерод). В данной работе приводятся также результаты экспериментальных исследований по конверсии природного газа (СН4 — 95 % об.), полученные на разработанной и созданной авторами установке.
Экспериментальная установка
Экспериментальная установка для конверсии природного газа в углерод и водород реализована в соответствии со схемой (рис. 1).
Основной элемент установки — проточный реактор выполнен двухкамерным. Одна из камер (2) представляет собой цилиндр из нержавеющей стали, в котором размещена кварцевая труба диаметром 54 мм, длиной 360 мм, заполненная металлическим катализатором. Вторая камера (3), разрядная, представляет собой отре-
зок коаксиальной линии с укороченным центральным проводником, переходящим в круглый волновод. В первой камере осуществляется нагрев катализатора, а в разрядной камере инициируется и поддерживается необходимый для осуществления конверсии природного газа СВЧ-разряд. В отличие от традиционного высокотемпературного пиролиза в данной установке нагрев катализатора осуществляется с использованием СВЧ-энергии от магнетронного генератора (1) с выходной мощностью 1,5 кВт на частоте 2450 МГц.
С целью развязки генератора с нагрузкой (катализатором) и измерения уровня отраженной мощности использован циркулятор (на рисунке не показан). Для контроля температуры катализатора по высоте реактора выполнены три кварцевых окна (4). Контроль температуры осуществлялся с помощью пирометра типа «Кельвин» с пределами измерения 200-2000 °С. Природный газ подавался в нижнюю часть реактора, а подвод СВЧ-энергии для воздействия на катализатор осуществлен сверху посредством волноводно-коаксиального перехода (ВКП). С помощью точно такого же ВКП осуществлен подвод СВЧ-энергии в разрядную камеру от второго СВЧ-гене-ратора с выходной мощностью 2 кВт (магнетрона), подключенного к разрядной камере через циркулятор. Для сбора продуктов плазмохимической реакции предусмотрены агломератор (5) и система фильтров (6). Из системы фильтров углерод собирается в сборнике углерода. Водород и остаточный газ с помощью вытяжной вентиляции выбрасывался в атмосферу.
Эндотермическая реакция
75 кДж/моль разложения метана на углерод и водород осуществлялась в описываемой установке следующим образом.
На первом этапе металлический катализатор (Fe, Ni, TiNi) нагревается с помощью СВЧ-энергии в токе азота до температуры ~560 °С за счет диссипативных потерь. Это значение лежит в диапазоне температур, характерном для традиционного термического катализа. Затем в реактор подавался холодный (~30 °С) природный газ (метан ~97 %) с
расходом 0,161,0 м 3/ч а с, отключалась подача азота и зажигался СВЧ-разряд в
разрядной камере. При этом происходило снижение температуры катализатора до значений 450-480 °С в зависимости от расхода метана. О начале реакции судили по снижению температуры в реакторе и появлению водорода в выходных газах. Одновременно велось визуальное наблюдение за ходом реакции через кварцевое окно разрядной камеры по наличию углерода. Наработанные продукты реакции транспортировались через систему фильтров в сборники углерода и водорода. Для этого аппарат работал при незначительном разряжении.
Плазмохимическая конверсия метана, реализованная в установке, происходит, по нашему мнению, следующим образом. На разогретом катализаторе происходит предварительное возбуждение молекул метана и реакция образования непредельных углеводородов (этилена и ацетилена), которые газовым потоком транспортируются в разрядную камеру, где и осуществляется, собственно, плазменный катализ. Факелом плазмы продукты реакции выносятся в постреакторное пространство.
Продукты реакции анализировались с использованием рентгеновского дифрактометра XRD-6000, хромат-рографа «Хроматэк-Кристалл 5000», прибора для определения удельной поверхности «Sorbi», растрового электронного микроскопа «Philips SEW 515», водородного газоанализатора «ИВА-18».
Результаты исследований
Для выяснения роли и степени влияния плазмы СВЧ-разряда на эффективность процесса была проведена серия опытов на холодном катализаторе с СВЧ-разрядом и на горячем катализаторе как при наличии, так и в отсутствие СВЧ-разряда. Для исследования был использован природный газ (СН4 95-97 %) Мыльджинского
ГКМ, предоставленный ОАО «Томск-газпром».
Для того чтобы оценить роль катализатора в конверсии природного газа, в отсутствие плазмы СВЧ-разря-да была исследована зависимость степени конверсии, выход углеродно-
В отличие от традиционного высокотемпературного пиролиза в данной установке нагрев катализатора осуществляется с использованием СВЧ-энергии от магнетронного генератора
40 ГАЗОХИМИЯ
■ НАШ САЙТ В ИНТЕРНЕТЕ: WWW.GAZOHIMIYA.RU
НАНОТЕХНОЛОГИИ Я
го материала и водорода от температуры катализатора при постоянном
Зависимость степени конверсии от температуры катализатора
приведены степень конверсии и концентрации водорода и побочных продуктов реакции (С2+ — углеводородов) V °С Расход газа, м3/ч KCh5, % Концентрация Н2, % об. Содержание С2+-углеводородов, % об.
с использованием в качестве катали- 350 0,16 2,56 1,5 5,54
затора железа (Fe). 400 0,16 3,06 2,2 5,60
Из этих результатов следует, что при 450 0,16 4,27 2,6 2,58
данных условиях эксперимента степень конверсии и выход водорода
составляют единицы процентов и уве- 1Табл. 2 1
личиваются с ростом температуры. При этом не был зафиксирован сколь- Результаты влияния СВЧ-разряда на ход плазмохимической реакции
ко-нибудь значительный выход углерода, а содержание С2+-углеводородов с ростом температуры уменьшается, V °С Расход газа, м3/ч KCh5, % Концентрация Н2, % об. Содержание С2+-углеводородов, % об.
что, возможно, связано с образовани- 15 0,16 68,6 13,88 1,87
ем при высоких температурах жидкой фракции углеводородов. Для выяснения влияния СВЧ-разря- 15 0,43 48,4 16,09 3,0
15 1,08 19,7 13,48 2,52
да на ход плазмохимической реакции
были проведены эксперименты на И Табл. 3 1
холодном катализаторе при различных расходах газа. Их результаты представлены в табл. 2. Приведенные результаты показывают, что под воздействием только плаз- Параметры процесса конверсии природного газа
Тср, °С Расход газа, м3/ч KCh5, % Концентрация Н2, % об. Содержание С2+-углеводородов, % об.
мы СВЧ-разряда на порядок увеличива- 350 0,16 58,1 13,1 0,35
ется степень конверсии по сравнению с 450 0,16 71,4 15,95 0,15
термическим катализом, реализованным в предыдущем опыте (см. табл. 1). В 560 0,16 76,0 16,0 1,5
данном случае наряду с водородом, С2+-
углеводородами наблюдалось образо- |Табл. 4 1
вание углеродного материала.
Анализ показал, что углеродный материал состоит из углеродных нанотрубок (УНТ), фуллеренов и аморфного углерода. Степень конверсии уменьшается с увеличением расхода газа, а между концентрацией водорода, содержанием С2+-углево-дородов, с одной стороны, и расходом газа, с другой, такой зависимости не наблюдается.
В табл. 3 приведены параметры процесса конверсии природного газа, концентрации водорода и побочных продуктов реакции при совмещенном воздействии нагретого металлического катализатора и плазмы СВЧ-разря-да. Эксперименты проводились при разных температурах катализатора и постоянном расходе газа.
Эксперименты, проведенные при совмещенном действии катализатора и плазмы СВЧ-разряда, показали, что при этих условиях возрастает степень конверсии газа (до 80 %), выход водорода (до 16 %) и углеродного материала. В его состав входят: углеродные многослойные, однослойные, луковичные нанотрубки с удельной поверхностью от 30 до 100 м2/г; аморфный углерод с удельной поверхностью 200-400 м2/г. Размер
Соотношение аморфного углерода и нанотрубок от используемых катализаторов
Состав катализатора Содержание нанотрубок углерода и размер по ОКР Содержание аморфного углерода,
% нм %
TiNi 46,13 9,12 45,00
AlNi 33,14 10,57 55,00
Ni 56,51 7,12-14,92 21,24
Fe 78,24 3,70-12,40 4,04
Mo 24,91 26,26-37,22 64,89
Ti 23,05 5,8-11,6 —
Типы образующихся нанотрубок и их размеры
Состав катализатора MWCNT, % (размер по ОКР, нм) SWCNT, % (размер по ОКР, нм) Onions, % (размер по ОКР, нм)
Ni 19,4 (14,9) 45,0 (7,8) 35,6 (7,1)
Fe 28,2 (12,4) 38,8 (7,3) 33,0 (3,7)
Mo 47,0 (26,3) 32,9 (37,2) 20,1 (37,2)
В зависимости от используемого катализатора получается наноуглеродный материал различной структуры и размеров
Табл. 1
Табл.5
ГАЗОХИМИЯ 41
Я НАНОТЕХНОЛОГИИ
частиц аморфного углерода составлял от 10 до 50 нм. Поперечный размер нанотрубок в зависимости от условий процесса изменялся в пределах от 5 до 27 нм.
В зависимости от используемого катализатора получается наноуглеродный материал различной структуры и размеров (табл. 4 и 5).
Как видно из табл. 4, углеродный продукт преимущественно состоит из аморфного углерода, углеродных нанотрубок. Присутствует также небольшое количество графита и ортакарбона. Ортакарбон образуется только на никельсодержащих катализаторах — Ni, AlNi и TiNi. Химический состав катализатора значительно влияет на количество образующихся нанотрубок, их соотношение и размеры (табл. 5).
Варьируя скорости подачи сырья и материал засыпки, можно получать углеродный материал с различным соотношением нанотрубок и амофно-го дисперсного углерода. При этом изменяется удельная поверхность углеродного продукта. На рис. 2 представлены микрофотографии углерода, на которых видно, что полученный продукт можно условно разделить на два вида.
Рис. 2а представляет собой ассо-циаты «ватной» текстуры размерами 10-20 мкм, состоящие из более мелких структур размерами 200-250 нм, минимально обнаруженные частицы, образующие неупорядоченные ассо-циаты, имеют размеры 30-40 нм. Вероятно, это и есть аморфный углерод. Вторая структура образующегося углерода — это нановолокна и нанотрубки, которые могут быть хаотично переплетены между собой (рис. 2б) или перераспределены на поверхности «ватных» ассоциатов. К сожалению, возможности прибора не позволили детально изучить более мелкие формы полученного углерода, который явно присутствует в углеродном продукте.
Совмещение каталитических процессов с плазмохимическими процессами приводит к сложным зависимостям в эндотермической реакции разложения метана. Сокращение времени контакта с катализатором при сохранении постоянной линейной скорости метана уменьшает конверсию метана и концентрацию водорода, концентрация С2+ углеводородов постоянна (рис. 3 и 4). Увеличение линейной скорости метана сильно снижает конверсию метана, выход водорода и увеличивает концентра-
Рис. 2
Микрофотографии образцов углерода
(а) (б)
Рис. 3
Зависимость конверсии метана от времени контакта
Рис. 4
Зависимость концентрации газообразных продуктов от времени контакта
ксн4.-C2h3
42 ГАЗОХИМИЯ
■ НАШ САЙТ В ИНТЕРНЕТЕ: WWW.GAZOHIMIYA.RU
НАНОТЕХНОЛОГИИ
цию С2+ углеводородов в реакционных газах.
Используемые катализаторы относятся к «массивным металлам» и представляют собой гранулы размером 0,1-2 мм. При воздействии на катализатор СВЧ-поля между гранулами за счет наведенных электромагнитных полей возникают частичные электрические разряды (микроразряды), создающие начальную концентрацию свободных электронов. В потоке газа они инициируют СВЧ-газовый разряд и приводят к образованию плазменной струи на выходе из реактора, подпитываемой СВЧ-энергией. Температура в плазменной струе может достигать 5000 К. Кроме этого, благодаря образованию микроразрядов не происходит отложение углерода на поверхности катализатора, что позволяет увеличить срок работы катализатора. Наличие этих «инициаторов» обеспечивает возникновение и поддержание СВЧ-разряда при малых уровнях СВЧ-мощности. В условиях газового разряда с образованием плазменной струи происходят быстрые химические превращения природного газа (метана), в частности в углерод и водород. Конверсия метана зависит от типа катализатора, размера его составляющих частиц, температуры в реакторе и уровня СВЧ-мощности, подаваемой в активную зону реактора. В нашем случае использовался непрерывный режим работы СВЧ-генератора с плавно регулируемой выходной мощностью в пределах 700-1500 Вт. Проведенные измерения отраженной от катализатора и прошедшей на нагрузку СВЧ-мощности при СВЧ-разряде и без него показали, что реакция идет «штатно» (с фиксируемым выходом углерода) при уровне мощности, подаваемой на катализатор, около 1 кВт. Этот уровень мощности, возможно, превышает необходимый для проведения плазмохимической реакции по конверсии углеводородов в углерод и водород.
Таким образом, по нашему представлению, в описанном процессе налицо комбинированное воздействие СВЧ-излучения на объект.
Это и нагрев катализатора, и инициирование микроразрядов в катализаторе, возбуждающих атомы и молекулы газа и поддерживающих существование плазменной струи, с помощью которой осуществляется вынос продуктов конверсии из реакторного пространства.
Естественно, что данный вопрос требует дальнейшего, более глубокого изучения.
Заключение
В процессе исследования совмещенного воздействия нагретого металлического катализатора и плазмы СВЧ-разряда показано, что по сравнению с традиционным термическим катализом резко повышается (до 80%) степень конверсии природного газа, увеличивается выход водорода и наноуглеродного материала в виде нанотрубок (однослойных и многослойных, луковичных), не содержащих окклюдированных частиц металла, в отличие от всех других способов получения наноуглерода [6]. Значительная концентрация водорода в выходящих
Варьируя скорости подачи сырья и материал засыпки, можно получать углеродный материал с различным соотношением нанотрубок и амофного дисперсного углерода
газах делает перспективным данный способ конверсии для получения как наноуглеродного материала, так и водорода в промышленных масштабах. В то же время несоответствие концентраций водорода (16 %) и С2+-углероводородов (1,5 %) со степенью конверсии природного газа (76 %) предполагает образование жидких углеводородов (бензол) при данном способе конверсии природного газа и требует дополнительных исследований.
В ходе экспериментов обнаружено, что в отличие от традиционного термического катализа в рассматриваемом процессе конверсии практически не происходит зауглероживания катализатора. Предположительно это можно объяснить существованием (возникновением) между частицами катализатора микроразрядов под действием СВЧ-поля, которые «зачищают» поверхность катализатора, увеличивая тем самым срок его химической активности.
Работа выполнена при финансовой поддержке ФЦП «Научные и научнопедагогические кадры инновационной России» на 2009-2013 гг. ЁЗ
СПИСОК ЛИТЕРАТУРЫ
1. Пармон В.Н. Распределение температуры в грануле дисперсного тела при неравновесном выделении тепла внутри гранулы. Стационарный случай // Кинетика и катализ. — 1996. — Т. 37. — № 3. — С. 476.
2. Федосеев В.И., Аристов Ю.И., Танашев Ю.Ю., Пармон В.Н. Пиролиз метана под действием импульсного СВЧ-излучения в присутствии твердых катализаторов // Кинетика и катализ, 1996. — Т. 37. — № 6. — С. 869-872.
3. Бабарицкий А.И., Герасимов Е.Н., Демкин С.А., Животов В.К. и др. Импульсно-периодический СВЧ-разряд как катализатор химической реакции // ЖТФ, 2000. — Т. 70. — Вып. 11. — С. 36-41.
4. Жерлицын А.Г., Шиян В.П., Галанов С.И.и др. Получение высокодисперсного углеродного материала из природного газа под действием СВЧ-излучения // Известия вузов. Физика, 2007. -№ 10/3. — С. 280-284.
5. Патент РФ № 2317943. Способ получения углерода и водорода из углеводородного газа и устройство для его осуществления / Ю.В. Медведев,
А.Г. Жерлицын и др. — Опубл. 27.02.2008 г., Бюл. № 6.
6. Раков Э.Г. Методы непрерывного производства углеродных нановолокон и нанотрубок // Химическая технология, 2003. — № 10. — С. 2-7.
ГАЗОХИМИЯ 43
Паровая конверсия
Паровая конверсия — получение чистого водорода из лёгких углеводородов (например метана, пропан-бутановой фракции) путём каталитической конверсии углеводородов в присутствии водяного пара.
Знания специалистов нашей компании позволяют проектировать, строить и эксплуатировать установки по производству водорода для снабжения водородом Заказчика. Мы разрабатываем установки производства водорода методом парового реформинга от 300 до 200000 Нм3/час.
На рисунке показана стандартная технологическая схема для высокопроизводительной водородной установки.
Основные этапы процесса
1. Гидродесульфурация исходного сырья
2. Паровой риформинг
3. Утилизация тепла для генерации пара
4. Конверсия СО
5. Очистка водорода с помо¬щью короткоцикловой адсорбции
Описание процесса
Очистка сырья
Природный газ подается на установку, разделяясь на два потока: один служит топливом к горелкам печи риформинга, а второй служит сырьевым газом для технологического процесса. В последний поток дозируется водород из блока КЦА, после чего он подается на всас сырьевых компрессоров.
Альтернативным сырьем может служить жидкая нафта, испаренная за счет тепла технологического газа.
Гидродесульфуризация
После этого смесь сырьевого газа и водорода (сырьевой газ) проходит через секцию гидродесульфуризации. В блоке гидроочистки, с применением катализатора органические соединения серы преобразуются в h3S, с гидрогенизацией всех содержащихся олефинов. В секции десульфуризации полученный h3S оседает в виде сульфида цинка на катализаторе. h3S является ядом для катализатора риформинга.
Риформинг
Десульфурированный сырьевой газ смешивается с перегретым паром. Далее, эта смесь проходит по катализаторным трубам в печи риформинга с горелками.
В трубах печи риформинга углеводороды и пар дополнительно нагреваются в присутствии катализатора, с получением водорода, углекислого газа, угарного газа. Горячий технологический газ выходит из трубок с катализатором установки риформинга при температуре около 850°C и поступает в парогенератор отходящих продуктов установки риформинга при температуре около 820°C, где производится пар для процесса, а температура на выходе регулируется согласно заданной температуре на входе в блок конверсии СО.
Конверсия СО
Из парогенератора отходящих продуктов установки риформинга технологический газ выходит с температурой около 343°C и поступает в емкость преобразовательного конвектора. В конвертере происходит реакция пара и угарного газа в присутствии катализатора с образованием водорода и углекислого газа.
К моменту выхода из конвертера температура газа увеличивается приблизительно на 70°C; это увеличение температуры варьируется в зависимости от производительности установки. Технологический газ выходит из конвертера при температуре около 410°C; выходная температура варьируется в зависимости от производительности установки.
Выходящий из конвертера технологический газ поступает в технологическую часть подогревателя сырья, где технологический газ охлаждается, одновременно подогревая сырьевой газ. Часть синтез-газа может направляться в обход нагревателя сырья с целью поддержания заданной температуры сырья для установки гидроочистки.
Технологический газ с выхода подогревателя сырья может использоваться для испарения нафты, если таковая подается в качестве сырья в установку. Затем технологический газ пропускается парогенератором тепла продуктов конвертера и теплообменник котловой воды для рекуперации тепла. Излишки генерируемого пара могут отводиться в заводскую сеть Заказчика. Далее технологический газ охлаждается, содержащаяся в потоке влага конденсируется перед подачей в сепаратор холодного конденсата, где конденсат отделяется от потока технологического газа перед вводом технологического газа в систему КЦА.
Система очистки водорода
В системе очистки КЦА применяется процесс адсорбции для получения водорода высокой чистоты. В каждом адсорбере находится слой оксида алюминия, углерод и молекулярное сито. Система работает по повторяющемуся циклу из двух этапов: адсорбция и регенерация.
Во время адсорбции технологический газ проходит через емкость адсорбера, где адсорбенты удаляют из него примеси.
В конце этапа адсорбции адсорбент насыщается примесями, после чего начинается этап регенерации (снижение давления, продувка и восстановление давления). Полученный остаточный газ собирается в емкости остаточного газа и используются в качестве первичного топлива в установке риформинга.
Утилизация отходящего тепла
Весь получаемый пар вырабатывается за счет утилизации тепла. Пар вырабатывается парогенератором дымовых газов, парогенератором отходящих продуктов установки риформинга и парогенератором тепла продуктов конвертера, входящими в состав установки. Для защиты системы получения пара предусмотрена химическая обработка котловой воды.
Тепло дымовых газов используется также для перегрева технологического сырья и воздуха для горения для печи риформинга.
Установки производства водорода методом паровой конверсии метана широко используются в следующих отраслях промышленности
— Пищевая промышленность
— Сталелитейная промышленность
— Стекольная промышленность
— Производство удобрений
— Производство метанола
— Производства электроники
— Производство перекиси водорода
— Процессы нефтеперерабатывающих заводов
— Процессы гидрогенизации/Продукты переработки масел
Центр данных по альтернативным видам топлива: производство и распределение водорода
Несмотря на то, что водород присутствует в большом количестве на Земле как элемент, он почти всегда присутствует в составе другого соединения, такого как вода (H 2 O) или метан (CH 4 ), и его необходимо разделить на чистый водород (H 2). ) для использования в электромобилях на топливных элементах. Водородное топливо соединяется с кислородом воздуха через топливный элемент, создавая электричество и воду в результате электрохимического процесса.
Производство
Водород можно производить из различных внутренних источников, включая ископаемое топливо, биомассу и электролиз воды с помощью электричества. Воздействие водорода на окружающую среду и энергоэффективность зависят от того, как он производится. Реализуется несколько проектов по снижению затрат, связанных с производством водорода.
Есть несколько способов производства водорода:
Риформинг / газификация природного газа: Синтез-газ, смесь водорода, окиси углерода и небольшого количества двуокиси углерода, образуется в результате реакции природного газа с высокотемпературным паром.Окись углерода реагирует с водой с образованием дополнительного водорода. Этот метод самый дешевый, эффективный и самый распространенный. На конверсию природного газа с использованием пара приходится большая часть водорода, ежегодно производимого в Соединенных Штатах.
Синтез-газ также может быть создан путем реакции угля или биомассы с высокотемпературным паром и кислородом в газификаторе под давлением, который преобразуется в газообразные компоненты — процесс, называемый газификация . Полученный синтез-газ содержит водород и монооксид углерода, который реагирует с водяным паром для отделения водорода.
Электролиз: Электрический ток расщепляет воду на водород и кислород. Если электричество производится из возобновляемых источников, таких как солнце или ветер, образующийся водород также будет считаться возобновляемым и имеет множество преимуществ по выбросам. Набирают обороты проекты по производству водорода, когда избыточная возобновляемая электроэнергия, если таковая имеется, используется для производства водорода посредством электролиза.
Возобновляемый жидкий риформинг: Возобновляемое жидкое топливо, такое как этанол, реагирует с высокотемпературным паром с образованием водорода вблизи точки конечного использования.
Ферментация: Биомасса превращается в сырье, богатое сахаром, которое можно ферментировать для получения водорода.
Ряд методов производства водорода находится в стадии разработки:
Основными производителями водорода являются Калифорния, Луизиана и Техас. Сегодня почти весь водород, производимый в Соединенных Штатах, используется для очистки нефти, обработки металлов, производства удобрений и обработки пищевых продуктов.
Основной задачей производства водорода является снижение стоимости технологий производства, чтобы сделать получаемый водород конкурентоспособным по сравнению с обычным транспортным топливом.Государственные и промышленные научно-исследовательские и опытно-конструкторские проекты снижают стоимость, а также снижают воздействие на окружающую среду технологий производства водорода. Узнайте больше о производстве водорода в Управлении технологий производства водорода и топливных элементов.
Распределение
Большая часть водорода, используемого в Соединенных Штатах, производится там или поблизости от того места, где он используется, обычно на крупных промышленных предприятиях. Инфраструктура, необходимая для распределения водорода по общенациональной сети заправочных станций, необходимых для повсеместного использования электромобилей на топливных элементах, все еще нуждается в развитии.Первоначальное развертывание транспортных средств и станций сосредоточено на построении этих распределительных сетей, в первую очередь в южной и северной Калифорнии.
В настоящее время водород распределяется тремя способами:
Трубопровод: Этот наименее дорогой способ доставки больших объемов водорода ограничен, поскольку в настоящее время доступно только около 1600 миль трубопроводов США для доставки водорода. Эти трубопроводы расположены недалеко от крупных нефтеперерабатывающих и химических заводов в Иллинойсе, Калифорнии и на побережье Мексиканского залива.
Трубные прицепы высокого давления: Транспортировка сжатого водородного газа грузовиком, железнодорожным вагоном, кораблем или баржей в трубчатых прицепах высокого давления является дорогостоящей и используется в основном на расстояния до 200 миль или меньше.
Цистерны для сжиженного водорода: Криогенное сжижение — это процесс, при котором водород охлаждается до температуры, при которой он становится жидкостью. Хотя процесс сжижения является дорогостоящим, он позволяет транспортировать водород более эффективно (по сравнению с использованием трубных прицепов высокого давления) на большие расстояния грузовиком, железнодорожным вагоном, кораблем или баржей.Если сжиженный водород не используется с достаточно высокой скоростью в точке потребления, он выкипает (или испаряется) из резервуаров для хранения. В результате необходимо тщательно согласовывать скорость доставки и потребления водорода.
Создание инфраструктуры для распределения и доставки водорода на тысячи будущих заправочных станций представляет собой множество проблем. Поскольку водород содержит меньше энергии на единицу объема, чем все другие виды топлива, его транспортировка, хранение и доставка к месту конечного использования обходятся дороже в пересчете на галлоновый эквивалент бензина (на ГПЭ).Строительство новой сети водородных трубопроводов связано с высокими начальными капитальными затратами, а свойства водорода создают уникальные проблемы для материалов трубопроводов и конструкции компрессора. Однако, поскольку водород можно производить из самых разных ресурсов, региональное или даже местное производство водорода может максимально использовать местные ресурсы и минимизировать проблемы с распределением.
Необходимо учитывать компромисс между централизованным и распределенным производством. Производство водорода централизованно на крупных заводах снижает производственные затраты, но увеличивает затраты на сбыт.Производство водорода в точке конечного использования — например, на заправочных станциях — снижает затраты на сбыт, но увеличивает производственные затраты из-за затрат на создание производственных мощностей на месте.
Государственные и промышленные научно-исследовательские проекты преодолевают препятствия на пути к эффективному распределению водорода. Узнайте больше о распределении водорода в Управлении технологий водорода и топливных элементов.
Производство водорода из метана более чистым и дешевым способом — ScienceDaily
Керамическая мембрана, разработанная группой исследователей из Испании, Норвегии и Америки, позволяет производить сжатый водород из метана с практически нулевыми потерями энергии.
Исследователи из Института химической технологии (ITQ), Политехнического университета Валенсии (UPV) и Высшего совета научных исследований (CSIC) разработали керамические мембраны, которые позволяют производить сжатый водород из метана более чистым и дешевым способом. Результаты исследования находят широкое применение в транспортных средствах на водородных топливных элементах, а также в химической промышленности, поскольку этот новый метод позволяет производить водород из метана и электроэнергии всего за один этап и с почти нулевыми потерями энергии.
Водород — отличное топливо, которое благодаря своей высокой энергетической плотности и нулевому выбросу парниковых газов играет важную роль в большом количестве промышленных процессов. Его сочетание с кислородом в атмосфере производит энергию и воду в качестве единственного побочного продукта, что делает его одним из основных кандидатов на замену ископаемым видам топлива в качестве источника энергии для транспортного сектора.
Профессор исследования CSIC и руководитель исследования Хосе Мануэль Серра объясняет, что «разработка и внедрение на рынок гибридных и электромобилей позволит нам снизить влияние транспорта на выбросы CO2 в ближайшие годы и, как следствие, на тепличную среду. влияние на планету.Следующим естественным шагом, о чем свидетельствуют инвестиции, сделанные крупными брендами автомобильной промышленности, является внедрение автомобилей на водородном топливе, которые обладают большей автономностью и заряжаются быстрее, чем электрические ».
Исследователи ITQ разработали газоразделительный мембранный реактор с электронным управлением и позволяющий эндотермически производить водород с практически нулевыми потерями энергии.
«Наши исследования показывают, что можно получить сжатый водород всего за один этап с высокой эффективностью из электричества, метана или биогаза и одновременно изолировать CO2, не выбрасывая его в атмосферу.Наш метод позволяет производить водород под высоким давлением распределенным образом, что означает, что его можно производить на автозаправочных станциях, в жилых районах, гаражах или фермах. Используя электричество из возобновляемых источников, наша система позволяет нам производить водород с очень низким углеродным следом. Мы также можем хранить оставшуюся возобновляемую энергию в виде сжатого водорода для дальнейшего использования, когда потребность в электроэнергии возрастет, или в качестве топлива для транспортных средств », — добавляет Серра.
Работа исследователей ITQ, разработанная совместно с Университетом Осло и американской транснациональной компанией CoorsTek, позволит заряжать автомобили с водородным топливным элементом с энергетической эффективностью и простотой, как у электромобиля с аккумулятором. .Благодаря метану, как первичному источнику энергии, имеющему заметно более низкую стоимость, чем электричество, водород может быть более дешевым топливом для транспортных средств, чем электричество.
История Источник:
Материалы предоставлены Asociación RUVID . Примечание. Содержимое можно редактировать по стилю и длине.
Производство водорода — Управление энергетической информации США (EIA)
Как производится водород?
Чтобы произвести водород, он должен быть отделен от других элементов в молекулах, в которых он находится.Есть много различных источников водорода и способов его производства для использования в качестве топлива. Двумя наиболее распространенными методами производства водорода являются паровой конверсии метана и электролиз (разделение воды на электричество. Исследователи изучают другие методы.
Процессы производства водорода
Источник: Министерство энергетики США, Управление энергоэффективности и возобновляемых источников энергии, Производство водорода (общественное достояние)
Нажмите для увеличения
Паровой риформинг метана — широко используемый метод получения коммерческого водорода
Паровой риформинг метана составляет почти весь коммерчески производимый водород в Соединенных Штатах.Коммерческие производители водорода и нефтеперерабатывающие заводы используют паровой риформинг метана для отделения атомов водорода от атомов углерода в метане (Ch5). При паровом риформинге метана высокотемпературный пар (от 1300 ° F до 1800 ° F) под давлением 3–25 бар (1 бар = 14,5 фунтов на квадратный дюйм) реагирует с метаном в присутствии катализатора с образованием водорода, окиси углерода. , и относительно небольшое количество диоксида углерода.
Природный газ является основным источником метана для производства водорода промышленными предприятиями и нефтеперерабатывающими заводами.Свалочный газ / биогаз, который можно назвать биометаном , является источником водорода для нескольких электростанций на топливных элементах в Соединенных Штатах. Биотопливо и нефтяное топливо также являются потенциальными источниками метана.
Электролиз использует электричество
Электролиз — это процесс отделения водорода от воды с помощью электрического тока. Электролиз обычно используется для демонстрации химических реакций и производства водорода на уроках естественных наук в средней школе. В крупном промышленном масштабе процесс может упоминаться как power-to-gas , где power — электричество, а водород — газ .Сам по себе электролиз не производит никаких побочных продуктов или выбросов, кроме водорода и кислорода. Электроэнергия для электролиза может поступать из возобновляемых источников, таких как гидроэнергия, солнечная энергия или энергия ветра. Если электричество для электролиза производится из ископаемого топлива (уголь, природный газ и нефть) или сжигания биомассы, то соответствующее воздействие на окружающую среду и выбросы углекислого газа косвенно связаны с электролизом.
Другие способы получения водорода
- Использование микробов, которые используют свет для производства водорода
- Преобразование биомассы в газ или жидкость и отделение водорода
- Использование технологий солнечной энергии для отделения водорода от молекул воды
Категории водорода
Производители водорода, продавцы, государственные учреждения и другие организации могут классифицировать или определять водород в соответствии с источниками энергии для его производства.Например, водород, произведенный с использованием возобновляемых источников энергии, может называться возобновляемым водородом или зеленым водородом . Водород, полученный из угля, может называться коричневым водородом , а водород, полученный из природного газа или нефти, может называться серым водородом . Производство коричневого или серого водорода в сочетании с улавливанием и хранением / секвестрацией углерода может обозначаться как синий водород .
Последнее обновление: 7 января 2021 г.
Преобразование природного газа в водород без выбросов углерода
Увеличить / Трудно поверить, что это может сократить выбросы углерода.Бум добычи природного газа сыграл важную роль в сокращении выбросов углерода в США, поскольку метан, основной компонент природного газа, при сжигании выделяет больше энергии на каждый атом углерода, чем другие ископаемые виды топлива. Но в каждой молекуле метана все еще есть атом углерода, поэтому переход на природный газ в конечном итоге приведет к уменьшению отдачи, когда дело доходит до сокращения выбросов. Чтобы сохранить умеренный климат, нам в конечном итоге придется отказаться и от природного газа.
Но две новые статьи, вышедшие на этой неделе, предполагают, что мы можем использовать природный газ, не сжигая его. В них подробно описаны эффективные методы преобразования метана в водород, позволяющие улавливать большую часть или весь оставшийся углерод. Затем водород можно было сжечь или преобразовать в электричество в топливных элементах, в том числе в мобильных топливных элементах, используемых в автомобилях. Подача, полученная из метана, также может быть объединена с водородом из других источников.
Используемая технология также довольно крутая сама по себе, включая такие вещи, как катализаторы, растворенные в жидком металле, и твердые материалы, которые позволяют току проходить через них в виде протонов, а не электронов.
Вариант 1: протонная проводимость
Метан — это просто атом углерода, связанный с четырьмя атомами водорода (CH 4 ). Эти углерод-водородные связи занимают промежуточное положение по стабильности между горючими водородно-водородными связями и чрезвычайно стабильными молекулами, которые образуются в результате его горения, двуокиси углерода и воды. Поэтому перегруппировка его связей для высвобождения водорода требует тщательно продуманной термодинамики.
Один из лучших вариантов — смешивание метана и пара при высоких температурах.В этих условиях вы разбиваете воду, что крайне невыгодно с энергетической точки зрения. Но вы образуете углекислый газ, что благоприятно, и вы получаете водород как из метана, так и из воды. Проблема в том, что вы получаете смесь двух газов, оба под низким давлением, что делает выход менее полезным в качестве топлива без обширной обработки.
РекламаЧтобы решить эту проблему, испано-норвежская команда обратилась к технологии, о существовании которой я даже не подозревал: твердому протонопроводящему электролиту.Электролиты — это просто материалы, которые позволяют заряженным ионам проходить через них; Хотя в основном это жидкости, для батарей было разработано несколько твердых электролитов. В этом случае электролит специфичен для протонов, ионизированной формы атома водорода. Другой способ рассматривать это как проводящий материал, который позволяет зарядам перемещаться по нему в форме протонов, а не электронов.
Ключевой особенностью этого приложения является то, что если вы приложите разность напряжений к этому материалу, ионы водорода, образующиеся в результате реакции метана с паром, будут переходить на другую сторону, где они могут образовывать молекулы водорода.Чтобы еще больше улучшить ситуацию, авторы покрыли одну сторону материала никелем, который катализирует реакцию метана с паром.
Когда этот материал используется для изготовления стенок реакционной камеры, вы в конечном итоге получаете сжатый водород с менее чем четырьмя частями на миллион примесей снаружи камеры. Его можно сжечь или отправить в топливный элемент. Внутри вы получаете концентрированный углекислый газ, смешанный с небольшим количеством пара. Углерод от сжигания метана по существу улавливается, и полученный материал готов к хранению, а это означает, что это может быть технология с чрезвычайно низким уровнем выбросов.
Авторы также отмечают, что эта технология хорошо масштабируется. Они представляют себе небольшой реактор, подключенный к линии природного газа в доме, который за ночь подает водород в автомобиль на топливных элементах. Отработанное тепло от рабочих условий реактора при 800 градусах Цельсия можно было использовать для обогрева дома или обеспечения горячей водой. Обратной стороной является то, что углекислый газ, производимый в этом варианте использования, почти наверняка попадет в атмосферу.
Вариант 2: реакции в жидком металле
Недавно мы обсуждали случай, когда исследователи разработали химические реакции, протекающие на поверхности жидкого металла, что обеспечивает довольно специфические условия реакции.Теперь американо-индийская команда обнаружила, что можно удалить метан из водорода, используя реакцию, которая протекает внутри жидкого металла.
РекламаЦель состоит в том, чтобы решить проблему для другого типа реакции метана, при которой непосредственно удаляется водород, а твердый углерод остается. Есть множество металлов, которые могут катализировать эту реакцию, но все они страдают от серьезной проблемы: углерод образуется на их поверхности, в конечном итоге забивая катализатор, так что метан не может до него добраться.Эта проблема решается путем проведения реакции в жидком металле.
Идея состоит в том, чтобы взять каталитический металл и растворить его в виде сплава в металле, который является жидким в условиях реакции. И эти условия реакции горячие, более 1000 градусов по Цельсию, так что вы не ограничены только металлами, которые находятся в жидком состоянии при температуре около комнатной. Затем через каталитический сплав барботируют метан, при этом пузырьки превращаются в почти чистый водород к тому времени, когда они достигают поверхности. Углерод, который обычно загрязняет катализатор, не может покрыть отдельные атомы в сплаве, и поэтому в конечном итоге он собирается и всплывает наверх.
Авторы протестировали различные растворители (индий, висмут, свинец, серебро и др.), А также никелевые, медные и платиновые катализаторы. Они обнаружили, что комбинация никеля и висмута является наиболее эффективным катализатором. При 1065 градусах Цельсия одного метра столба жидкого металла было достаточно, чтобы преобразовать 95 процентов введенного метана в водород, и казалось, что выходы будут расти с более длинными колоннами. Метан также не является проблемой для большинства топливных элементов, поэтому это не серьезная проблема загрязнения.
Эксплуатация колонки в течение 170 часов показала, что она работает по плану — каталитическая активность не снижается. И, как и ожидалось, углерод просто всплыл наверх, и его можно было снять. Он действительно собрал небольшие брызги металла от пузырьков, вырывающихся на поверхность, но кратковременного погружения углерода в металл было достаточно, чтобы удалить это. Хотя углерод можно было изолировать, просто выбросив его в любое удобное место, он был в основном в форме графита и мог использоваться для изготовления таких вещей, как конденсаторы или карандаши.
Оба этих подхода, очевидно, будут ограничивать количество энергии, доступной из метана, по сравнению с простым его сжиганием, поскольку они требуют высоких температур, чтобы реакции работали. Но почти наверняка наступит время, когда выбросы углерода из природного газа будут считаться проблемой, и они, кажется, действительно обеспечивают решение этой проблемы, позволяя нам продолжать использовать метан еще долгое время после того, как мы попытаемся постепенно отказаться от ископаемого топлива.
Nature Energy , 2017.DOI: 10.1038 / s41560-017-0029-4
Science , 2017. DOI: 10.1126 / science.aao5023 (О DOI).
Оценка углеродного следа производства водорода
Когда-нибудь появится смысл заправлять автомобили водородом.
dpa / изображение альянса через Getty ImagesВодород — самый легкий и самый распространенный элемент во Вселенной. Его можно использовать как источник энергии, и он является важным сырьем для многих нефтехимических процессов.
При сгорании водород образует воду. Следовательно, водород можно использовать в качестве источника топлива с низким содержанием углерода. Водород можно сжигать напрямую или использовать в топливном элементе для производства электроэнергии.
Поскольку водород производит минимальное количество загрязняющих веществ при сгорании, многие считают его основным компонентом более чистой энергетики будущего. Президент Джордж Буш рекламировал потенциал «водородной экономики» в своем послании о положении страны в 2003 году. В попытку реализовать это видение были вложены миллиарды долларов.
Производство водорода
Но сначала нужно произвести водород. Более 95% мирового водорода производится с использованием процесса паровой конверсии метана (SMR). В этой реакции природный газ реагирует с паром при повышенной температуре с образованием моноксида углерода и водорода. Последующая реакция — реакция конверсии водяного газа — затем вступает в реакцию дополнительного пара с монооксидом углерода с образованием дополнительных водорода и диоксида углерода.
Реакция риформинга с метаном как:
CH 4 + H 2 O ⇌ CO + 3 H 2
Реакция водно-газовой конверсии (WGS):
CO + H 2 O ⇌ CO 2 + H 2
«Грязный секрет» водорода заключается в том, что он производится в основном из ископаемого топлива.Таким образом, действительно ли водород «чистый» зависит от метода производства.
Водород также можно получить путем электролиза воды, но это, как правило, более дорогостоящий подход, чем метод SMR. Когда электричество используется для производства водорода, термодинамика диктует, что вы всегда будете производить меньше энергии, чем потребляете.
Другими словами, потребляемая энергия в электричестве будет больше, чем выходная энергия водорода. Тем не менее, если доступен дешевый источник электроэнергии — например, избыток электроэнергии из сети в определенное время дня — производство водорода таким способом может оказаться экономичным.Это будет тема будущей статьи.
В любом случае, хотя сам водород при сжигании практически не загрязняет окружающую среду (могут образовываться некоторые оксиды азота или NOx), с ним связан углеродный след. Итак, давайте рассмотрим углеродный след водорода при его производстве с помощью обычного процесса SMR.
Процесс парового риформинга метана (SMR)
Современная установка SMR состоит из четырех систем: обессеривания, риформинга, высокотемпературного сдвига (HTS) и абсорбции при колебаниях давления (PSA).Эти системы отражают удаление серы, реакцию риформинга, реакцию WGS и очистку водорода.
Стадия обессеривания заключается в пропускании природного газа над катализатором. Эти системы обычно пассивны, и хотя с ними связаны незначительные выбросы углерода, они незначительны по сравнению с остальной частью системы.
Природный газ, поступающий в SMR, разделяется перед десульфуризацией, при этом небольшое количество потока смешивается с отходящим газом PSA и сжигается для обеспечения высоких температур, необходимых для реакции.
Основная часть природного газа обессеривается, смешивается с водяным паром и затем вступает в реакцию в установке риформинга. Реакция риформинга обычно происходит на катализаторе на основе никеля при повышенных давлениях и температурах.
Горячий газ, выходящий из SMR, охлаждается, при этом одновременно образуется пар. Затем к охлажденному газу в реакторе сдвига добавляют пар, чтобы преобразовать монооксид углерода в диоксид углерода и больше водорода.
Наконец, водород очищается в установке PSA.Это включает в себя этап повышения давления, который заставляет примеси связываться с адсорбентом, в то время как водород проходит через него. Когда адсорбент насыщается, давление снижается для удаления примесей, которые затем могут быть рециркулированы в качестве топливного газа.
Углеродный след парового риформинга метана
Углеродный след производства водорода с помощью SMR можно разделить на две части.
Во-первых, как показывают реакции SMR и WGS, 100% углерода в поступающем метане в конечном итоге превращается в CO 2 .В процессе производства одной молекулы CO 2 образуются четыре молекулы водорода (H 2 ), при этом пар вносит дополнительный водород.
Таким образом, на 1 миллион стандартных кубических футов (SCF) водорода, произведенного из метана, будет произведено 250 000 SCF CO 2 . В одной метрической тонне содержится 19 253 SCF диоксида углерода, поэтому из 1 миллиона SCF водорода будет произведено 13 метрических тонн диоксида углерода. Это будет, безусловно, самый большой углеродный след, связанный с процессом SMR.
Вторая часть — это углеродный след, связанный с отдельными технологическими установками. Должен быть произведен пар, реактор должен быть нагрет и т. Д. Но пар также создается, когда газ на выходе SMR охлаждается, так что это помогает компенсировать углеродную нагрузку.
Praxair LIN , один из крупнейших производителей водорода в мире, имеет разбитых выбросов углерода, связанных с отдельными этапами технологического процесса. Я преобразовал их данные в метрические тонны углекислого газа, выбрасываемого этими технологическими установками, на миллион SCF произведенного водорода.
- Энергия сжигания для риформинга — 3,7 метрических тонны
- Сжигание пара — 2,5 тонны
- Мощность сепарации и сжатия — 0,1 тонны
Если добавить это к диоксиду углерода, полученному в результате реакций с природным газом, общее количество полученного диоксида углерода составит 19,3 метрических тонн на миллион стандартных кубических футов водорода. Однако в документе Praxair отмечается, что это теоретический минимум. Из-за тепловых потерь и неэффективности фактическое количество на практике в большой водородной установке составляет 21.9 метрических тонн.
Преобразуется в 9,3 килограмма (кг) CO 2 , произведенного на 1 кг производства водорода. Один килограмм водорода — это энергетический эквивалент одного галлона бензина, из которого при сгорании выделяется 9,1 кг CO 2 .
Углеродный след часто указывается с точки зрения энергии. Например, электростанции обычно указывают углеродный след в киловатт-часах (кВтч). Один миллион стандартных кубических футов водорода содержит 79 100 киловатт-часов энергии.
Преобразуется в 0.28 кг выбросов углекислого газа, связанных с производством одного киловатт-часа водорода.
Конечно, это всего лишь углеродный след производства водорода. Чтобы использовать водород для производства энергии, его необходимо сжимать, транспортировать и либо сжигать, либо преобразовывать в электричество в топливном элементе. Сами топливные элементы также должны быть построены, и есть выбросы углерода, связанные с этими процессами строительства.
Для перспективы Управление энергетической информации перечисляет углеродный след производства электроэнергии из угля и природного газа как 1.0 кг / кВтч и 0,42 кг / кВтч соответственно. Но это для фактического преобразования в энергию, а не только для энергосодержания топлива.
В соотношении яблоки к яблокам это зависит от нескольких факторов, но вполне вероятно, что при преобразовании водорода в энергию углеродный след будет больше, чем у энергии, работающей на природном газе, но меньше, чем у энергии, работающей на угле. . Однако теоретически возможно улавливать выбросы углерода, образующиеся в процессе SMR.
Также возможно производить водород с использованием низкоуглеродных способов, которые исторически были менее экономичными.Это будет тема будущей статьи.
Текущее состояние и будущие разработки
Водород (H 2 ) в настоящее время используется в основном в химической промышленности для производства аммиака и метанола. Тем не менее, в ближайшем будущем ожидается, что водород станет важным топливом, которое в значительной степени будет способствовать повышению качества атмосферного воздуха. Водород как химический элемент (H) является наиболее распространенным на Земле, а молекулярный дигидроген (H 2 ) может быть получен из ряда возобновляемых и невозобновляемых источников с помощью различных процессов.До сих пор в мировом производстве водорода преобладали ископаемые виды топлива, при этом наиболее важными современными технологиями были паровые конверсии углеводородов (например, природного газа). Чистый водород также получают путем электролиза воды — энергоемкого процесса. В данной работе рассматриваются современные технологии, используемые для производства водорода (H 2 ) как из ископаемых, так и из возобновляемых ресурсов биомассы, включая риформинг (пар, частичное окисление, автотермический, плазменный и водный фазы) и пиролиз.Кроме того, обсуждаются другие методы получения водорода (например, электролиз воды) и методы очистки, такие как десульфурация и реакции конверсии водяного газа.
1. Введение
Водород — самый простой и самый распространенный элемент на Земле. Водород легко соединяется с другими химическими элементами и всегда находится в составе другого вещества, такого как вода, углеводород или спирт. Водород также содержится в природной биомассе, в которую входят растения и животные.По этой причине он считается энергоносителем , а не источником энергии.
Водород можно производить с использованием различных внутренних ресурсов, включая ядерную энергию, природный газ и уголь, биомассу и другие возобновляемые источники. К последним относятся солнечная, ветровая, гидроэлектрическая или геотермальная энергия. Такое разнообразие внутренних источников энергии делает водород перспективным энергоносителем и важным элементом энергетической безопасности. Желательно, чтобы водород производился с использованием различных ресурсов и технологических процессов или способов.Производство водорода может быть достигнуто с помощью различных технологических процессов, включая термические (риформинг природного газа, переработка возобновляемых жидкостей и бионефти, биомасса и газификация угля), электролитические (разделение воды с использованием различных энергетических ресурсов) и фотолитические (разделение воды. использование солнечного света через биологические и электрохимические материалы).
Годовое производство водорода оценивается примерно в 55 миллионов тонн, при этом его потребление увеличивается примерно на 6% в год.Водород можно получать разными способами из широкого спектра исходного сырья. В настоящее время водород в основном производится путем паровой конверсии природного газа, процесса, который приводит к массовым выбросам парниковых газов [1, 2]. Около 50% мирового спроса на водород в настоящее время формируется за счет парового риформинга природного газа, около 30% — за счет риформинга нефти / нафты из отходящих газов нефтеперерабатывающих заводов / химических промышленных предприятий, 18% — за счет газификации угля, 3,9% — за счет электролиза воды и 0,1% из других источников [3].Электролитические и плазменные процессы демонстрируют высокую эффективность получения водорода, но, к сожалению, они считаются энергоемкими процессами [4].
Фундаментальный вопрос заключается в разработке технологий производства водорода, альтернативных технологиям, основанным на ископаемом топливе, особенно для его использования в качестве топлива в транспортном секторе. С этой проблемой можно столкнуться при использовании альтернативных возобновляемых ресурсов и связанных с ними методов производства, таких как газификация или пиролиз биомассы, электролитический, фотолитический и термический крекинг воды.Однако невозможно рассматривать только экологическую перспективу, поскольку, например, фотолитический крекинг воды является экологически безопасным, но его эффективность для промышленного использования очень низка. Таким образом, очевидно, что процессы, которые необходимо учитывать, должны учитывать не только экологические проблемы, но и наиболее благоприятные экономические факторы.
2. Водород из ископаемого топлива
Технологии переработки ископаемого топлива преобразуют водородсодержащие материалы, полученные из ископаемых видов топлива, таких как бензин, углеводороды, метанол или этанол, в поток газа, обогащенного водородом.Сегодня переработка метана (природного газа) в качестве топлива является наиболее распространенной коммерческой технологией производства водорода. Большинство ископаемых видов топлива содержат определенное количество серы, удаление которой является важной задачей при планировании водородной экономики. В результате также будет обсуждаться процесс обессеривания. Кроме того, будет представлена недавно разработанная многообещающая технология плазменного риформинга.
Водородный газ можно производить из углеводородного топлива с помощью трех основных технологий: (i) паровой риформинг (SR), (ii) частичное окисление (POX) и (iii) автотермический риформинг (ATR).Эти технологии производят большое количество оксида углерода (CO). Таким образом, на последующем этапе один или несколько химических реакторов используются для значительного превращения CO в диоксид углерода (CO 2 ) посредством конверсии водяного газа (WGS) и реакций предпочтительного окисления (PrOx) или метанирования, которые описаны ниже. .
2.1. Паровой риформинг
Паровой риформинг в настоящее время является одним из наиболее распространенных и в то же время наименее дорогих процессов производства водорода [5]. Его преимущество заключается в высокой эффективности его работы и низких эксплуатационных и производственных затратах.Наиболее часто используемым сырьем являются природный газ и легкие углеводороды, метанол и другие кислородсодержащие углеводороды [6]. Схема реакций риформинга углеводородов и метанола, используемых в качестве сырья, следующая [7]:
Весь процесс состоит из двух этапов. На первом этапе углеводородное сырье смешивается с паром и подается в трубчатый каталитический реактор [8]. Во время этого процесса синтез-газ (газовая смесь H 2 / CO) производится с более низким содержанием CO 2 ((1) и (2)).Требуемая температура реакции достигается добавлением кислорода или воздуха для сжигания части исходного материала (греющего газа) внутри реактора. На втором этапе охлажденный газообразный продукт подается в каталитический нейтрализатор CO, где монооксид углерода в значительной степени превращается с помощью пара в диоксид углерода и водород (3). Каталитический процесс парового риформинга требует сырья, свободного от серосодержащих соединений, чтобы избежать дезактивации используемого катализатора.
Процесс SR требует умеренных температур, например, 180 ° C для метанола и кислородсодержащих углеводородов и более 500 ° C для большинства обычных углеводородов [9, 10].Используемые катализаторы можно разделить на два типа: неблагородные металлы (обычно никель) и драгоценные металлы из элементов VIII группы (обычно платина или родий). Из-за жестких ограничений массо- и теплопередачи обычные установки парового риформинга ограничены коэффициентом эффективности гранулированных катализаторов, который обычно составляет менее 5% [11]. Поэтому кинетика редко является ограничивающим фактором для обычных реакторов парового риформинга [12], и поэтому в промышленности используются менее дорогие никелевые катализаторы.
Важным фактором, характеризующим процесс SR, является соотношение атомов H: C в исходном материале. Чем выше это соотношение, тем меньше выделяется углекислый газ. Мембранный реактор может заменить оба реактора в обычном процессе SR для достижения общей реакции (2) [13]. Тепловой КПД производства водорода с помощью SR процесса метана в промышленных масштабах составляет около 70–85% [14]. Ряд других сырьевых материалов также возможно для достижения этой эффективности в ближайшем будущем, например, твердые коммунальные отходы, отходы пищевой промышленности, масла, целенаправленно выращиваемая или отработанная сельскохозяйственная биомасса, а также топливо ископаемого происхождения, такое как уголь.Недостатком является высокое производство CO 2 , ок. 7,05 кг CO 2 / кг H 2 .
2.2. Частичное окисление
Частичное окисление (POX) и каталитическое частичное окисление (CPOX) углеводородов было предложено для производства водорода для автомобильных топливных элементов и некоторых других коммерческих приложений [15, 16]. Газифицированное сырье может представлять собой метан и биогаз, но в первую очередь фракции тяжелой нефти (например, вакуумные остатки, топочный мазут), дальнейшая обработка и утилизация которых затруднены [17].POX — это некаталитический процесс, в котором сырье газифицируется в присутствии кислорода ((5) и (6)) и, возможно, пара ((7), ATR) при температурах в диапазоне 1300-1500 ° C и давлениях в диапазон 3–8 МПа. По сравнению с паровым риформингом (H 2 : CO = 3: 1) образуется больше CO (H 2 : CO = 1: 1 или 2: 1). Таким образом, процесс дополняется преобразованием CO с паром в H 2 и CO 2 . Эта реакция способствует поддержанию равновесия между отдельными продуктами реакции [18]:
Газовая смесь, образованная в результате частичного окисления, содержит CO, CO 2 , H 2 O, H 2 , CH 4 , сероводород (H 2 S) и оксисульфид углерода (COS).Часть газа сжигается, чтобы обеспечить достаточно тепла для эндотермических процессов. Сажа, образующаяся при разложении ацетилена как промежуточного продукта, является нежелательным продуктом. Его количество зависит от доли H: C в исходном топливном сырье. Поэтому, как и в случае с SR, была предпринята попытка перейти на сырье с более высоким соотношением H: C, например, на природный газ. Хотя эксплуатация реактора дешевле по сравнению с паровым риформингом, последующая конверсия делает эту технологию более дорогой.Поскольку процесс не требует использования катализатора, нет необходимости удалять сернистые элементы из природного газа, что снижает эффективность катализатора. Сернистые соединения, содержащиеся в газифицированном сырье, превращаются в сероводород (около 95%) и оксисульфид углерода (около 5%) [19].
Катализаторы могут быть добавлены в систему частичного окисления (CPOX) для снижения рабочей температуры, прибл. 700–1000 ° С. Однако контроль температуры оказывается затруднительным из-за образования кокса и горячих точек из-за экзотермического характера реакций [10, 15, 16, 20].Для конверсии природного газа катализаторы обычно основаны на Ni или Rh. Однако никель имеет сильную склонность к коксованию, и стоимость Rh значительно выросла. Krummenacher et al. [16] удалось использовать каталитическое частичное окисление декана, гексадекана и дизельного топлива. Высокие рабочие температуры (> 800 ° C) [16] и соображения безопасности могут затруднить их использование для практичных и компактных портативных устройств из-за регулирования температуры [21]. Обычно тепловой КПД реакторов POX с метаном в качестве топлива находится в диапазоне 60–75% [22].
2.3. Автотермический риформинг
Как упоминалось ранее, в автотермическом риформинге (ATR) пар добавляется в процессе каталитического частичного окисления. ATR представляет собой комбинацию реакций парового риформинга (эндотермических) и частичного окисления (экзотермических) [23]. Преимущество ATR состоит в том, что он не требует внешнего тепла, а также проще и дешевле, чем SR метана.
Диапазон работы топливного процессора для производства водорода показан на рисунке 1. Выбор условий работы установки риформинга зависит от конкретной цели.Основная цель — высокий выход водорода при низком содержании окиси углерода. Для парового риформинга возможны максимальная водородная эффективность и низкое содержание окиси углерода. Однако паровой риформинг — это эндотермический процесс и, следовательно, требует больших затрат энергии. Эта энергия должна передаваться в систему извне.
Еще одно существенное преимущество ATR перед процессом SR состоит в том, что его можно остановить и запустить очень быстро, производя при этом большее количество водорода, чем только POX [23].Есть некоторые ожидания, что этот процесс станет привлекательным для отрасли «газ-жидкость» из-за благоприятного состава газа для синтеза Фишера-Тропша, относительной компактности ATR, более низких капитальных затрат и потенциальной экономии за счет масштаба [24]. Для риформинга метана термический КПД сопоставим с КПД POX (около 60–75%) и немного меньше, чем у парового риформинга. Бензин и другие высшие углеводороды могут быть преобразованы в водород на борту для использования в автомобилях с помощью автотермического процесса с использованием подходящих катализаторов [25].
2.4. Сдвиг вода-газ, предпочтительное окисление и метанирование
В процессе риформинга образуется смесь продуктового газа со значительными концентрациями окиси углерода, часто 5 об.% Или более (около 10 об.%) [10]. Чтобы увеличить количество водорода, газообразный продукт пропускают через реактор конверсии водяного газа (WGS), чтобы уменьшить содержание монооксида углерода, одновременно увеличивая содержание водорода (3). Обычно желательна высокая температура, чтобы способствовать быстрой кинетике.Однако это приводит к высокой равновесной селективности по монооксиду углерода и снижению выхода водородного продукта. Таким образом, снижение содержания CO в синтез-газе достигается в двухстадийном процессе, который включает высоко- и низкотемпературную реакцию конверсии водяного газа, известную как процессы «HTS» и «LTS», соответственно (рис. 2). . На первом этапе, проводимом в интервале 310–450 ° C с использованием катализатора Fe 3 O 4 / Cr 2 O 3 , концентрация СО снижается с 10 до 3 об.%.На втором этапе, проводимом в диапазоне 180–250 ° C, содержание CO дополнительно снижается до низкого уровня 500 ppm с использованием катализаторов Cu / ZnO / Al 2 O 3 [26].
Для дальнейшего снижения содержания монооксида углерода в газообразном продукте используется реактор преференциального окисления (PrOx) или реактор селективного метанирования моноксида углерода [10, 27]. Иногда вместо предпочтительного окисления используется термин «селективное окисление». Селективное окисление относится к восстановлению монооксида углерода в топливном элементе, обычно топливном элементе с протонообменной мембраной (PEM), тогда как предпочтительное окисление происходит в реакторе вне топливного элемента [27].Реакторы PrOx и метанирования имеют свои преимущества и проблемы. Реактор предпочтительного окисления увеличивает сложность системы, поскольку в систему необходимо добавлять точные концентрации воздуха [10, 27]. Однако эти реакторы компактны, и если вводится избыточное количество воздуха, некоторое количество водорода сгорает.
Реакторы метанирования проще в том, что не требуется воздуха. Однако на каждый прореагировавший CO расходуется три молекулы H 2 . Кроме того, CO 2 реагирует с водородом, и необходимо поддерживать тщательный контроль условий в реакторе, чтобы минимизировать ненужное потребление водорода.В настоящее время преимущественное окисление является основным разрабатываемым методом [27]. Катализаторы обычно представляют собой благородные металлы, такие как платина, рутений или родий, нанесенные на Al 2 O 3 [10, 27]. В то же время, H 2 очищается с помощью альтернативных подходов, а именно адсорбции при переменном давлении, криогенной дистилляции и мембранных технологий, которые могут обеспечить необходимую чистоту водорода (около 98-99%). Наиболее выгодным методом очистки газов является адсорбция при переменном давлении из-за его высокой эффективности (> 99.99%) и гибкость.
2,5. Обессеривание
Как обсуждалось ранее, в настоящее время производство водорода происходит в основном за счет переработки природного газа, хотя благодаря значительным достижениям в топливных элементах повышенное внимание уделяется другим видам топлива, таким как метанол, пропан, бензин, и топливам для логистики, таким как как Jet-A, дизель и JP8 [28]. За исключением метанола, все эти виды топлива содержат некоторое количество серы, причем конкретные серосодержащие соединения зависят от типа и источника топлива.По этой причине обессеривание считается очень важным этапом в технологиях переработки топлива.
Процессы обессеривания можно классифицировать в зависимости от характера основного физико-химического процесса, используемого для удаления серы (рис. 3). Наиболее развитыми и коммерчески доступными являются технологии каталитического превращения сероорганических соединений с удалением серы. Такие технологии каталитической конверсии включают обычную гидродесульфуризацию (HDS), гидроочистку с использованием усовершенствованных катализаторов и / или конструкции реакторов, а также сочетание гидроочистки с некоторыми дополнительными химическими процессами для поддержания технических характеристик топлива [29, 30].Основной особенностью технологий второго типа является применение физико-химических процессов, отличных по природе от каталитического HDS, для отделения и / или преобразования сероорганических соединений из потоков нефтепереработки. Такие технологии включают, в качестве ключевого шага, дистилляцию, алкилирование, окисление, экстракцию, адсорбцию или их комбинацию [31].
2.6. Плазменный риформинг
В случае плазменного риформинга сеть реакций риформинга такая же, как и при обычном риформинге.Однако энергия и свободные радикалы, используемые для реакции риформинга, обеспечиваются плазмой, обычно генерируемой с помощью электричества или тепла [32–35]. Когда вода или пар впрыскиваются вместе с топливом, помимо электронов образуются радикалы H • , OH • и O • , что создает условия для протекания как восстановительных, так и окислительных реакций. . Технологии плазменного риформинга были разработаны для облегчения POX, ATR и парового риформинга, при этом большинство реакторов являются POX и ATR [35].По сути, существует две основные категории плазменного риформинга: термический и нетепловой [35].
Плазменные устройства, называемые плазмотронами, могут генерировать очень высокие температуры (примерно> 2000 ° C) с высокой степенью контроля с помощью электричества [32–35]. Вырабатываемое тепло не зависит от химии реакции, и оптимальные рабочие условия могут поддерживаться в широком диапазоне скоростей подачи и составов газа. Компактность установки плазменного риформинга обеспечивается высокой плотностью энергии, связанной с самой плазмой, и уменьшенным временем реакции, что приводит к короткому времени пребывания.Потоки богатого водородом газа могут быть эффективно получены в установках плазменного риформинга из различных углеводородных топлив (например, бензина, дизельного топлива, нефти, биомассы, природного газа и реактивного топлива) с эффективностью преобразования, близкой к 100% [32, 36]. Технология плазменного риформинга имеет потенциальные преимущества перед традиционными технологиями производства водорода [32–35]. Условия плазмы (например, высокие температуры, высокая степень диссоциации и значительная степень ионизации) могут использоваться для ускорения термодинамически благоприятных химических реакций без катализатора или обеспечения энергии, необходимой для протекания процессов эндотермического риформинга.Установки плазменного риформинга могут обеспечить ряд преимуществ, а именно компактность и малый вес (благодаря высокой удельной мощности), высокую эффективность преобразования, минимальную стоимость (простые металлические или угольные электроды и простые источники питания), быстрое время отклика (доли секунды), работа с широким спектром видов топлива, включая тяжелые углеводороды (сырая нефть) и «грязные» углеводороды (дизельное топливо с высоким содержанием серы). Эта технология может быть использована для производства водорода для различных стационарных применений, таких как распределенное и экологически чистое производство электроэнергии для топливных элементов [32].Его также можно использовать для мобильных приложений (например, для производства водорода на борту транспортных средств с топливными элементами) и для заправки топливом (например, стационарных источников водорода для транспортных средств).
Единственными недостатками плазменного риформинга являются зависимость от электричества и сложность работы при высоком давлении (требуется для процессов высокого давления, таких как производство аммиака). Высокое давление, хотя и достижимо, увеличивает эрозию электрода из-за снижения подвижности дуги и, следовательно, сокращает срок службы электрода [33].
3. Водород из возобновляемых источников
Водород может также производиться другими методами, кроме риформинга ископаемого топлива. Краткое описание подходов на основе биомассы (например, газификации, пиролиза и реформинга водной фазы) наряду с получением водорода из воды (например, электролиз, фотоэлектролиз и термохимическое расщепление воды) описано ниже.
3.1. Газификация биомассы
Ожидается, что в ближайшем будущем биомасса станет наиболее вероятным возобновляемым органическим заменителем нефти.Биомассу можно получить из широкого спектра источников, таких как отходы животноводства, твердые бытовые отходы, растительные остатки, древесные культуры с коротким севооборотом, сельскохозяйственные отходы, опилки, водные растения, виды травянистых растений с коротким оборотом (например, просо), макулатура, кукуруза. , и многие другие [37, 38].
Технология газификации, обычно используемая с биомассой и углем в качестве топливного сырья, очень зрелая и коммерчески используется во многих процессах. Это разновидность пиролиза, и поэтому он основан на частичном окислении исходного материала до смеси водорода, метана, высших углеводородов, монооксида углерода, диоксида углерода и азота, известной как «генераторный газ» [37].Процесс газификации обычно страдает низкой термической эффективностью, поскольку влага, содержащаяся в биомассе, также должна испаряться. Его можно проводить с катализатором или без него, а также в реакторе с неподвижным или псевдоожиженным слоем, причем последний реактор обычно имеет лучшую производительность [38]. Добавление пара и / или кислорода в процессе газификации приводит к получению «синтез-газа» с соотношением H 2 / CO 2/1, последний используется в качестве сырья для реактора Фишера-Тропша для получения высших углеводородов (синтетических бензин и дизельное топливо) или в реактор WGS для производства водорода [38].Перегретый пар (около 900 ° C) использовался для преобразования сухой биомассы для достижения высоких выходов водорода. Однако процесс газификации обеспечивает значительное количество «смол» (сложная смесь высших ароматических углеводородов) в газообразном продукте даже при работе в диапазоне 800–1000 ° C. Вторичный реактор, в котором используется кальцинированный доломит и / или никелевый катализатор, используется для каталитической очистки и повышения качества получаемого газа [38]. В идеале на этих газификационных установках следует использовать кислород; однако установка отделения кислорода является непомерно высокой для малых предприятий.Это ограничивает газификаторы использованием воздуха, что приводит к значительному разбавлению продукта, а также к образованию NO x . Для этой технологии необходимы недорогие и эффективные кислородные сепараторы. Для производства водорода можно использовать процесс WGS для увеличения концентрации водорода с последующим процессом разделения для получения чистого водорода [39]. Обычно реакторы газификации строятся в больших масштабах и требуют непрерывной подачи огромного количества материала. Они могут достигать КПД порядка 35–50% в зависимости от более низкой теплотворной способности [4].Одна из проблем этой технологии заключается в том, что для сбора большого количества биомассы на центральную перерабатывающую установку необходимо использовать огромное количество ресурсов. В настоящее время высокие логистические затраты на газификационные установки и удаление «смол» до приемлемых уровней для производства чистого водорода ограничивают коммерциализацию производства водорода на основе биомассы. Для этой технологии для рентабельного производства водорода может потребоваться дальнейшая разработка эффективных распределенных газификационных установок меньшего размера.
3.2. Пиролиз и копиролиз
Другим перспективным в настоящее время способом получения водорода является пиролиз или копиролиз. Органическое сырье нагревается и газифицируется при давлении 0,1–0,5 МПа в диапазоне 500–900 ° C [40–43]. Процесс происходит в отсутствие кислорода и воздуха, поэтому образование диоксинов практически исключено. Поскольку вода или воздух отсутствуют, оксиды углерода (например, CO или CO 2 ) не образуются, что устраняет необходимость во вторичных реакторах (WGS, PrOx и т. Д.).). Следовательно, этот процесс обеспечивает значительное сокращение выбросов. Однако, если присутствует воздух или вода (материалы не были высушены), будут произведены значительные выбросы CO x . Среди преимуществ этого процесса — топливная гибкость, относительная простота и компактность, чистый побочный продукт углерода и сокращение выбросов CO x [40–43]. Реакцию обычно можно описать следующим уравнением: [41]
По температурному диапазону процессы пиролиза делятся на низкие (до 500 ° C), средние (500–800 ° C) и высокие (более 800 ° C).Быстрый пиролиз — один из новейших процессов превращения органических материалов в продукты с более высоким содержанием энергии. Продукты быстрого пиролиза появляются во всех образующихся фазах (твердой, жидкой и газообразной). Одной из проблем с этим подходом является возможность загрязнения образующимся углеродом, но его сторонники утверждают, что это можно свести к минимуму с помощью соответствующей конструкции. Поскольку он имеет потенциал для более низких выбросов CO и CO 2 и может работать таким образом, чтобы извлекать значительное количество твердого углерода, который легко улавливается [41, 44], пиролиз может играть важную роль. в будущем.
Применение копролиза смеси угля с органическими отходами недавно вызвало интерес в промышленно развитых странах, поскольку оно должно ограничить и облегчить бремя отходов при удалении отходов (отходы и чистые пластмассы, резина, целлюлоза, бумага, текстиль, дерево) [45, 46]. Пиролиз и копиролиз — это хорошо разработанные процессы, которые могут быть использованы в промышленных масштабах.
3.3. Риформинг в водной фазе
Риформинг в водной фазе (APR) — это разрабатываемая технология для переработки кислородсодержащих углеводородов или углеводов возобновляемых ресурсов биомассы для производства водорода [47, 48], как показано на Рисунке 4.Реакции APR протекают при значительно более низких температурах (220–270 ° C), чем при обычном паровом риформинге алкана (около 600 ° C). Низкие температуры, при которых происходят реакции реформинга в водной фазе, сводят к минимуму нежелательные реакции разложения, обычно встречающиеся при нагревании углеводов до повышенных температур [49, 50]. Кроме того, реакция конверсии водяного газа (WGS) является благоприятной при тех же температурах, что и реакции APR, что позволяет генерировать H 2 и CO 2 в одном реакторе с низким содержанием CO.Напротив, типичные процессы парового риформинга требуют многоступенчатых или множественных реакторов для достижения низких уровней CO в газообразном продукте. Еще одно преимущество процесса APR состоит в том, что он устраняет необходимость испарения воды, что представляет собой значительную экономию энергии по сравнению с традиционными процессами парофазного риформинга с водяным паром. Большинство исследований до настоящего времени было сосредоточено на катализаторах группы VIII на носителе, в которых Pt-содержащие твердые вещества имеют наивысшую каталитическую активность. Катализаторы на основе никеля, несмотря на их более низкую активность, были оценены из-за низкой стоимости никеля [47].Сторонники этой технологии заявляют, что эта технология более удобна для эффективного и избирательного преобразования сырья биомассы в водород. Для глюкозы и гликолей сообщалось о концентрациях 10-60 мас.% В воде [51]. Выбор катализатора важен, чтобы избежать метанирования, которое является термодинамически выгодным, наряду с продуктами Фишера-Тропша, такими как пропан, бутан и гексан [48, 52]. Недавно Rozmiarek [53] сообщил о способе на основе риформинга в водной фазе, который достиг эффективности более 55% с сырьем, состоящим из 60 мас.% Глюкозы в воде.Однако катализатор оказался нестабильным при длительных испытаниях (200 суток эксплуатации) [53]. Наконец, из-за умеренного выхода за пределы пространства-времени эти реакторы имеют тенденцию быть довольно большими. Повышение активности и долговечности катализатора — это область, в которой можно добиться значительного прогресса.
3.4. Электролиз
Перспективным методом производства водорода в будущем может стать электролиз воды. В настоящее время этим процессом производится около 4% водорода во всем мире [2].Электролиз воды или ее разложение на водород и кислород — хорошо известный метод, который начал коммерчески использоваться уже в 1890 году.
Электролиз — это процесс, при котором постоянный ток, проходящий через два электрода в водном растворе, приводит к разрушению химических связей, присутствующих в молекуле воды, на водород и кислород:
Процесс электролиза происходит при комнатной температуре. Обычно используемый электролит при электролизе воды — серная кислота, а электроды — из платины (Pt), которая не вступает в реакцию с серной кислотой.Процесс экологически чистый, поскольку не образуются парниковые газы, а производимый кислород находит дальнейшее промышленное применение. Однако по сравнению с описанными выше способами электролиз является технологией, требующей высоких энергозатрат.
Энергетический КПД электролиза воды (химическая энергия, получаемая на поданную электрическую энергию) на практике достигает 50–70% [54]. По сути, это преобразование электрической энергии в химическую энергию в виде водорода с кислородом в качестве полезного побочного продукта.Наиболее распространенной технологией электролиза является щелочная технология, но были разработаны протонообменная мембрана (PEM) и твердооксидные электролизеры (SOEC) [55, 56]. Электролизеры SOEC являются наиболее электрически эффективными, но наименее развитыми. Технология SOEC связана с проблемами коррозии, уплотнений, термоциклирования и миграции хрома. Электролизеры PEM более эффективны, чем щелочные, и не имеют проблем с коррозией и уплотнением, как SOEC; однако они стоят дороже, чем щелочные системы. Щелочные системы являются наиболее развитыми и имеют самые низкие капитальные затраты.У них самый низкий КПД, поэтому у них самые высокие затраты на электроэнергию.
3.5. Фотоэлектролиз
Фотоэлектролиз — один из возобновляемых способов производства водорода, демонстрирующий многообещающую эффективность и стоимость, хотя он все еще находится в стадии экспериментальной разработки [57]. В настоящее время это наименее затратный и наиболее эффективный способ получения водорода из возобновляемых источников. Фотоэлектрод — это полупроводниковый прибор, поглощающий солнечную энергию и одновременно создающий необходимое напряжение для прямого разложения молекулы воды на кислород и водород.В фотоэлектролизе используется фотоэлектрохимическая (PEC) система сбора света для проведения электролиза воды. Если полупроводниковый фотоэлектрод погружен в водный электролит, подвергающийся воздействию солнечного излучения, он будет генерировать достаточно электроэнергии, чтобы поддерживать возникающие реакции водорода и кислорода. При генерации водорода электроны выделяются в электролит, тогда как для генерации кислорода требуются свободные электроны. Реакция зависит от типа полупроводникового материала и интенсивности солнечного излучения, в результате чего плотность тока составляет 10–30 мА / см 2 .При этих плотностях тока необходимое для электролиза напряжение составляет примерно 1,35 В.
Фотоэлектрод состоит из фотоэлектрических (полупроводниковых), каталитических и защитных слоев, которые можно моделировать как независимые компоненты [58]. Каждый слой влияет на общую эффективность фотоэлектрохимической системы. Фотоэлектрический слой изготовлен из светопоглощающих полупроводниковых материалов. Поглощение света полупроводниковым материалом прямо пропорционально характеристикам фотоэлектрода.Полупроводники с широкими полосами обеспечивают необходимый потенциал для расщепления воды [54].
Каталитические слои фотоэлектрохимического элемента также влияют на характеристики электролиза и требуют подходящих катализаторов для расщепления воды. Слой оболочки — еще один важный компонент фотоэлектрода, который предотвращает коррозию полупроводника внутри водного электролита. Этот слой должен быть очень прозрачным, чтобы обеспечивать максимальную солнечную энергию, чтобы он мог достигать фотоэлектрического полупроводникового слоя.
3.6. Термохимическое расщепление воды
Термохимические циклы разрабатывались еще с 1970-х и 1980-х годов, когда они должны были внести свой вклад в поиск новых источников производства альтернативных видов топлива во время нефтяного кризиса. При термохимическом расщеплении воды, также называемом термолизом, только тепло используется для разложения воды на водород и кислород [59]. Считается, что с помощью этих процессов можно достичь общей эффективности, близкой к 50% [60].
Одноступенчатая термическая диссоциация воды описывается следующим образом:
Один из недостатков этого процесса связан с необходимостью эффективной техники разделения H 2 и O 2 , чтобы избежать образования взрывоопасной смеси.Для этого могут быть использованы полупроницаемые мембраны на основе ZrO 2 и других жаропрочных материалов. Разделение также может быть достигнуто после охлаждения газовой смеси продукта до более низких температур. Затем для эффективного отделения водорода можно использовать палладиевые мембраны.
Хорошо известно, что вода будет разлагаться при 2500 ° C, но материалы, стабильные при этой температуре, а также устойчивые источники тепла не являются легкодоступными. Поэтому были предложены химические реагенты для понижения температуры, тогда как в литературе упоминается более 300 циклов расщепления воды [61].Все процессы значительно снизили рабочую температуру до уровня ниже 2500 ° C, но обычно требуют более высокого давления. Однако считается, что масштабирование процессов может привести к повышению термического КПД, преодолевая одну из основных проблем, с которыми сталкивается эта технология. Кроме того, лучшее понимание взаимосвязи между капитальными затратами, термодинамическими потерями и термической эффективностью процесса может привести к снижению затрат на производство водорода [60].
4. Экономические аспекты производства водорода
В настоящее время наиболее широко используемым и дешевым методом производства водорода является паровой риформинг метана (природного газа) .Этот метод включает около половины мирового производства водорода, а цена на водород составляет около 7 долларов за ГДж. Сравнимую цену на водород обеспечивает частичное окисление углеводородов. Однако парниковые газы, образующиеся в результате термохимических процессов, должны улавливаться и храниться, и, таким образом, необходимо учитывать увеличение цены на водород на 25–30% [62].
Используемые далее термохимические процессы включают газификацию и пиролиз биомассы. Цена на водород, полученный таким образом, примерно в три раза выше, чем цена на водород, полученный способом SR.Следовательно, эти процессы обычно не считаются экономически выгодными по сравнению с паровым риформингом. Цена на водород от газификации биомассы колеблется в пределах 10–14 долларов США / ГДж, а на пиролиз — 8,9–15,5 долларов США / ГДж. Это зависит от оборудования, наличия и стоимости сырья [1].
Электролиз воды — одна из простейших технологий получения водорода без побочных продуктов. Электролитические процессы можно отнести к категории высокоэффективных. С другой стороны, стоимость входящей электроэнергии относительно высока и играет ключевую роль в цене получаемого водорода.
К 2030 году преобладающими методами производства водорода будут паровой риформинг природного газа и катализируемая газификация биомассы . В относительно небольшой степени будут использоваться как газификация угля, так и электролиз. Использование солнечной энергии в данном контексте сомнительно, но также возможно. Вероятно, к 2050 году роль солнечной энергии возрастет [1].
5. Выводы
Существует огромное количество исследований, направленных на развитие технологий производства водорода (H 2 ).В настоящее время наиболее развитой и используемой технологией является риформинг углеводородов. Чтобы уменьшить зависимость от ископаемого топлива, рассматриваются важные разработки в других технологиях генерации H 2 из возобновляемых ресурсов, таких как биомасса и вода. В таблице 1 приведены технологии, а также их использованное сырье и полученная эффективность. Важно отметить, что H 2 можно производить из широкого разнообразия сырья, доступного почти повсюду. В стадии разработки находится множество процессов с минимальным воздействием на окружающую среду.Развитие этих технологий может снизить зависимость мира от топлива, поступающего в основном из нестабильных регионов. «Собственное» производство H 2 может повысить как энергетическую, так и экономическую безопасность страны. Способность H 2 производиться из широкого разнообразия сырья и с использованием самых разнообразных процессов может сделать каждый регион мира способным производить большую часть своей собственной энергии. Очевидно, что по мере развития и развития технологий H 2 может оказаться наиболее распространенным доступным топливом.
| ||||||||||||||||||||||||||||||||||||||||||||
Очистка водорода не включена. |
Номенклатура
APR: | Водно-фазовый риформинг |
ATR: | Автотермический риформинг |
CPOX | 905 905 905 905 905 частичное окисление|
PEC: | Фотоэлектрохимический |
PEM: | Протонообменная мембрана |
POX: | Частичное окисление |
PrOx: | |
PrOx: | 905EC 905 905 Твердый оксид 9096 Твердый оксид 9095|
SR: | Паровой риформинг |
WGS: | Переход водогазовый. |
Благодарности
Авторы выражают признательность Исследовательскому комитету Кипрского университета и Кипрскому фонду содействия исследованиям за их финансовую поддержку в разработке фундаментальных исследований технологий каталитического производства водорода.
Что такое зеленый водород? И почему мы должны начать его использовать
Водород — нетоксичный бесцветный газ, даже если его называют зеленым водородом. Это самый распространенный элемент — по оценкам, 90% всех атомов составляют атомы водорода, составляющие около трех четвертей общей массы во Вселенной.
Но вам может быть интересно, как производится зеленый водород, и представляет ли зеленый водород реальную возможность революционизировать способы производства и использования энергии, особенно если мы продолжаем стремиться к тому, чтобы стать более экологически чистыми за счет сокращения выбросов углерода.
Как образуется водород?
На Земле нет природных месторождений водорода, его нужно извлекать из других соединений химическим способом. Подавляющее большинство промышленного водорода в настоящее время производится из природного газа с помощью процесса, известного как паровой риформинг метана или SMR.Получение водорода таким способом иногда называют коричневым, серым или даже голубым водородом!
Производство зеленого водорода
Водород можно также получить путем электролиза воды (с использованием электрического тока для разложения воды H 2 O на составляющие ее элементы, такие как водород и кислород). Если этот электрический ток вырабатывается возобновляемым источником (например, солнечными фотоэлектрическими батареями или ветряной турбиной), полученный чистый водород известен как зеленый водород.
Каковы
побочные продукты производства водорода?Паровой риформинг метана (SMR) реагирует на метан в природном газе с высокотемпературным паром в присутствии катализатора.Это производит водород и, в конечном итоге, углекислый газ, CO2. Поскольку природный газ относительно дешев, производимый водород также относительно дешев. Однако стандартный процесс SMR имеет существенный недостаток, заключающийся в выбросе большого количества CO2 в атмосферу, CO2, как хорошо известно, является очень значительным парниковым газом. Менее известно, что метан сам по себе имеет потенциал глобального потепления, который в 85 раз выше, чем CO2, поэтому любая небольшая утечка метана из его источника и в ходе технологического процесса также является значительным фактором изменения климата.Неограниченное производство водорода с использованием SMR является серьезной проблемой в наших попытках избежать климатической катастрофы.
Улавливание и хранение углерода — CCS
В качестве лучшей альтернативы были предложены варианты паровой конверсии метана, при которых CO2 улавливается и хранится в стабильной форме в другом месте (улавливание и хранение углерода — CCS). УХУ вполне может быть работоспособным, однако есть сомнения в нашей способности управлять хранением уловленного углерода и финансировать его в течение будущих десятилетий и, возможно, столетий или даже тысячелетий.К сожалению, у нас нет хорошей репутации в управлении огромными отложениями углерода, которые мы унаследовали. Торфяные болота и вересковые пустоши в Великобритании являются огромными хранилищами и выбросами углерода, и наше руководство вызывает серьезную озабоченность: https://www.bbc.co.uk/news/uk-472
Зеленый водородОпределение зеленого водорода
Если возобновляемая энергия (например, от солнечных панелей) используется для выработки электроэнергии для электролиза воды, то зеленый водород может производиться без каких-либо вредных выбросов.
Наша способность производить большие количества зеленого водорода будет играть важную роль в обеспечении альтернативы ископаемому топливу, поскольку мы переходим к низкому уровню выбросов и работаем над чистой, здоровой окружающей средой. Поскольку электромобили становятся все более и более популярными, нам необходимо переосмыслить нашу стратегию производства электроэнергии, если мы собираемся поддержать увеличивающееся количество водителей электромобилей, которые будут в пути и должны будут заряжать свои электромобили.